Liquid silicone rubber,LSR VS Mixed Silicone Rubber(HTV)
What is the difference with LSR (liquid silicone rubber)and mixed silicone rubber?
LSR and mixed Silicone Rubber are the two most commonly used material process options for molded silicone products. The two have completely different shapes, processing methods, and application fields, and each has its own advantages in production efficiency, quality, cost, and applicable scenarios. Liquid silicone rubber and solid silicone rubber can be distinguished by making process, appearance, smell , molding process, industry useful and cost.Accurately understanding their differences can not only help engineers and purchasers select the right material, help brand marketing scientific positioning, but also significantly reduce communication costs and development risks. Contact Z.S.R, Our group have the silicone material engineer and expert support you choose the fited material for your silicone project needs.
What is silicone Rubber?
Silicone rubber refers to a rubber whose main chain is composed of alternating silicon and oxygen atoms, and the silicon atom is usually connected to two organic groups. Ordinary silicone rubber is mainly composed of siloxane chains containing methyl and a small amount of vinyl. The introduction of phenyl can improve the high and low temperature resistance of silicone rubber, while the introduction of trifluoropropyl and cyano can improve the heat and oil resistance of silicone rubber. Silicone rubber has good low temperature resistance and can generally work at -55°C. After the introduction of phenyl, it can reach -73°C. The heat resistance of silicone rubber is also outstanding. It can work for a long time at 180°C, and can withstand several weeks or more at a temperature slightly higher than 200°C and still be elastic. It can instantly withstand high temperatures above 300°C. Silicone rubber has good air permeability and the oxygen permeability is the highest among synthetic polymers. In addition, silicone rubber also has the outstanding characteristics of physiological inertness and does not cause coagulation, so it is widely used in the medical field.
Silicone rubber is divided into heat vulcanization type (high temperature vulcanized silicone HTV) and room temperature vulcanization type (RTV), among which the room temperature vulcanization type is further divided into polycondensation reaction type and addition reaction type. High temperature silicone rubber is mainly used to manufacture various silicone rubber products, while room temperature silicone rubber is mainly used as adhesive, potting material or mold. The hot vulcanized type has the largest usage, and the hot vulcanized type is divided into methyl silicone rubber (MQ), methyl vinyl silicone rubber (VMQ, the largest usage and product brand), methyl vinyl phenyl silicone rubber PVMQ (low temperature resistance, radiation resistance), and others include nitrile silicone rubber, fluorosilicone rubber, etc.
What is Liquid silicone rubber?
Liquid silicone is relative to solid high temperature vulcanized silicone rubber. It is a liquid rubber with good fluidity, fast vulcanization, safer and more environmentally friendly, and can fully meet food grade requirements. Liquid silicone, also known as liquid silicone, is a liquid rubber relative to solid high-temperature vulcanized silicone rubber. It has the characteristics of good fluidity, fast vulcanization, safer and more environmentally friendly,Wide temperature range (-40°C-380°C )and can fully meet food grade requirements.
Liquid silicone has excellent tear resistance, resilience, anti-yellowing, thermal stability, heat resistance and anti-aging. It is a highly transparent and safe food-grade material. Liquid silicone rubber (LSR) is a two-component silicone material consisting of A and B. It is mixed in a static mixer and then injected into a mold for molding.No auxiliary materials such as vulcanizers are added during molding, and the molding is done by sealed feeding.
The types of liquid silicone rubber?
- Injection molding liquid silicone rubber (LSR): The full name is injection molding liquid silicone rubber, and the vulcanization equipment is an injection molding machine. The injection molding machine has a very simple process (no need for manual processes such as batching, refining, cutting, and placing in the high-temperature glue process, only one worker is needed to take the product), high product precision (all manual procedures before molding are replaced by machines), high output (A/B glue is mixed and molded in a few seconds at a certain temperature), saving manpower, electricity, and materials. It can produce all products produced by high-temperature glue and will be a mainstream of silicone rubber material development in the next few years.
- Mold silicone rubber (RTV-2): used for crafts and low-alloy molding molds.
- Electronic silicone rubber (RTV-T): used for moisture-proof, insulating backlight panels and heat dissipation materials for electrical components.
- Sealant (RTV-1): commonly known as glass glue, used for building sealing, waterproofing projects, aluminum bonding, electronics and lighting, etc.
Liquid silicone rubber can be used for trademarks, products, pacifiers, medical supplies, coating, impregnation and infusion, etc. It is used for molding molds, injection molding processes, cake molds and other silicone products of crystal glue, polyurethane, epoxy resin, etc. It is widely used as moisture-proof, shipping, insulation coating and potting materials for electronic components in the electronics industry, and it plays a role in dustproof, moisture-proof, shockproof and insulation protection for electronic components and assemblies. If transparent gel is used to pot electronic components, it can not only play a role in shockproof and waterproof protection, but also the components can be seen and the fault of the components can be detected with a probe, and replaced. The damaged silicone gel can be potted and repaired again. It can also be used to manufacture molding molds for products made of materials such as gypsum, wax, epoxy resin, polyester resin, polyurethane resin and low-melting-point alloys, and is used in high-frequency embossing of artificial leather, surface and bottom modeling of shoes, manufacturing of arts and crafts, ceramics, toy industry, furniture, replication of household appliances and electronic components, as well as molding of gypsum and cement materials, molding of wax products, manufacturing of models, and molding of materials.
Z.S.R group have the capability capability for producing silicone toolings, producing HTV Silicone products, LSR molded silicone products, Molded multi-colored Silicone products. We also can Custom silicone toolings,Custom silicone molding,Custom Silicone compression molding, Custom LSR molding, Custom silicone Dripping injection dispensing (co-injection) , Custom silicone fabric coating and curing molding. If you need any compression molding for mixed silicone rubber project or LSR molding for liquid silicone rubber project, please contact our expert.
The advantage of liquid silicone rubber
What is Solid silicone rubber
Solid silicone rubber is a saturated polymer elastic material,Solid silicone is in solid state and has no fluidity. It is also a transparent environmentally friendly material. During molding, vulcanizing agent needs to be added to speed up the vulcanization molding time and open mold casting is used for molding.
Mixed silicone rubber is a non-crosslinked rubber compound formed by adding reinforcing fillers, incremental fillers and functional additives to polyorganosiloxane as the base rubber compound and mixing it in a rubber mixer.
Core characteristics Basic materials: Linear polymers containing methyl or vinyl groups are used as raw rubber, combined with white carbon black, silicone oil and other compounding agents.
Temperature range: It can work for a long time at -60℃ to +250℃, and has the characteristics of high and low temperature resistance, ozone resistance, arc resistance, etc.
Processing technology: It needs to be formed at a temperature of 140-165℃ through the action of a vulcanizing agent, and adopts a dual curing system, which is suitable for compression molded products
Core characteristics of solid silicone rubber: stable structure, strong physical properties with the characteristics of high and low temperature resistance, can work for a long time at -60℃~+250℃ solvent resistance, crack resistance, anti-adhesion, electrical insulation, chemical resistance, ozone resistance, weather resistance, good electrical properties, strong resistance to corona, arc, and electric sparks, chemical stability, weather aging resistance, radiation resistance, physiological inertness, and good air permeability etc. It has a wide range of applications , suitable for thick-walled or large parts.
The advantage of solid silicone rubber
Liquid silicone rubber and solid silicone rubber can be distinguished by appearance, making process, smell, molding process, industry useful and cost.
Appearance
Liquid silicone rubber
Liquid silicone rubber is in a liquid state and has fluidity; It is a highly transparent and safe food-grade material. No auxiliary materials such as vulcanizers are added during molding, and the molding is done by sealed feeding.
Solid silicone rubber
Solid silicone rubber is in a solid state and has no fluidity. Solid silicone is in solid state and has no fluidity. It is also a transparent environmentally friendly material. During molding, vulcanizing agent needs to be added to speed up the vulcanization molding time and open mold casting is used for molding.
Making process
Liquid silicone rubber Making process
The production of liquid silicone rubber mainly includes 3 steps: raw material preparation, processing and preparation, and post-treatment.Liquid silicone is mainly composed of siloxane (chemical formula R3SiO1/2), which is made by heating reaction after adding crosslinking agent and catalyst. Among them, the raw materials of siloxane are mainly silicon dioxide and dimethyl silicon hydroxide. After high-temperature reaction, these substances form polymers, namely siloxane.
The production process steps of liquid silicone are as follows:
- Raw material preparation
The main raw materials of liquid silicone rubber are silane monomers and crosslinkers.
Silane monomers are organic compounds containing silicon bonds, such as methyltrimethoxysilane, phenyltrimethoxysilane, etc.
Crosslinkers are chemical substances that can induce crosslinking reactions in silane monomers, such as sodium hydroxide, alkyl trisilicon, etc.
During the production process, it is necessary to determine the appropriate ratio of silane monomers and crosslinkers according to different product requirements, and obtain a uniform raw material mixture through strict weighing and mixing.
- Processing and preparation
After the raw material mixture enters the processing equipment, it first needs to be mixed and homogenized.
The purpose of mixing and homogenization is to fully mix the silane monomers and crosslinkers in the raw material mixture to avoid local excess or deficiency, which affects the subsequent reaction process.
Mixing and homogenization are usually carried out using a high shear mixer or agitator, and the time and speed need to be adjusted according to the specific product requirements.
After mixing and homogenization, the raw material mixture enters the reactor for reaction.
The reactor usually adopts a tank reactor or a tubular reactor, and the reaction temperature and time need to be adjusted according to the specific product requirements.
During the reaction, the silane monomer and the crosslinking agent undergo a crosslinking reaction to form a three-dimensional network structure, and the liquid silicone rubber begins to form.
After the reaction, heat treatment or pressure treatment is required to make the crosslinking reaction more stable and ensure the stable performance of the product.
- Post-treatment
After the reaction is completed, the liquid silicone rubber needs to be post-treated, including filtration, degassing, drying and other steps.
The purpose of filtration is to remove the solid impurities remaining in the reactor to ensure the purity of the product.
The purpose of degassing is to remove the bubbles in the liquid silicone rubber to avoid affecting the performance of the product.
The purpose of drying is to remove the moisture in the liquid silicone rubber to keep it stable.
In short, the production of liquid silicone rubber requires strict control of the raw material ratio, mixing and homogenization, reaction process and post-treatment to ensure the stable quality of the product.
Through the above steps, liquid silicone with different hardness and viscosity can be obtained.
Liquid Silicone is liquid shape before being formed, and has fluidity, fast vulcanization, environmental protection and safety. It can meet the requirements of food grade certification, and has the advantages of tearing strength, resilience, heat yellowing and thermal stability.
Liquid silicone is divided into encapsulated silicone rubber, silicone rubber mold, sealant and other types of liquid silicone, divided into A glue and B glue, using quantitative device to control both of 1:1 ratio, and then through the static mixer to fully mixing, injection feeding pipe after injection molding production.
The liquid silica gel was injected into the hot runner mold and made of silica gel products, which can achieve the advantages of one molding, no waste and automation.
The main point of Liquid silicone rubber
Liquid silicone is a transparent, elastic, high and low temperature resistant and aging resistant material with the following
Characteristics:
- Resistance to steam and humidity
- Flame retardancy
- Low creep and compression set
- Weatherability
- Vibration absorption
- Corrosion resistance
- Resistance to mold, mildew, and bacteria growth
High and low temperature resistance: Liquid silicone can be used in a temperature range of -60℃ to +200℃, and will not deform, crack or stick due to heat or cold.
Aging resistance: Liquid silicone is not easily affected by oxygen, ultraviolet rays, moisture and other factors in the natural environment, and will not harden or deform due to aging.
Tensile strength: Liquid silicone has high tensile strength and can maintain its shape and elasticity under tension and pressure.
Food grade certification: Liquid silicone material can pass food grade certification and is suitable for use in food packaging and other related fields.
After mixing A / B at 20 C, the safe operation time in the sealed state is 5 days, and the safe operation time is shortened when the temperature rises.
Liquid silicone can be cured at room temperature and can be cured at high temperature. The curing process can be completed in a few seconds by high temperature curing. Liquid silicon rubber is a typical liquid silicon rubber, which is soft, nontoxic, tasteless and transparent. Medical safety is the high safety of food.
Solid silicone rubber Making process
Fumed silica gel
Fumed silica gel is prepared by the gas phase method (also known as pyrolysis or chemical vapor deposition). The specific steps are as follows:
Raw materials: The silicon source is usually silicon tetrachloride (SiCl4) or silane (SiH4).
Process: Under high temperature environment, the silicon source gas reacts with oxygen or ammonia to produce silica particles, which are then cooled and collected in an inert gas.
Precipitated silica gel
Precipitated silica gel is prepared by the precipitation method (also known as the wet method or liquid phase method). The specific steps are as follows:
Raw materials: The silicon source is usually a silicate solution.
Process: By adding an acid or alkaline solution, the silicate ions in the silicate solution undergo a precipitation reaction to produce silica gel. The precipitate is filtered, washed, dried and calcined to obtain the final product.
Mixing silica gel is one of the synthetic processes of silica gel, which is generally completed through the following steps:
- Material mixing
Mix various raw materials such as silicone oil and put them into the rubber mixer for mixing. The temperature is controlled below 40 degrees Celsius. Turn on the cooling water and maintain a stable powder feeding speed. The mixing time of each batch of rubber is about 20 to 40 minutes. No other impurities or rubber particles can be mixed in the mixing production process. If it is an open mill operation, a dustproof or exhaust device should be installed above the roller of the open mill to reduce the export and flying of white carbon black affecting the workshop environment; the mixing operation of the internal mixer is relatively closed, which can improve production efficiency, reduce labor intensity, and reduce the floating and flying of white carbon black, but it is not strict with the interval time. The mixing time of each batch of rubber is about 8 to 18 minutes, and the filling factor of the internal mixer should be controlled in the range of 0.7 to 0.75. The discharge temperature is related to the type of filler and should usually be controlled in the range of 50℃ to 70℃.
- Heating treatment
When fumed silica is used as a reinforcing agent, its surface is not surface modified. The structure control agent added to the rubber is further combined with the silica surface (Si-OH) by heating treatment to eliminate low molecular volatiles in the rubber. It is usually treated at 160℃~200℃ in a nitrogen or reduced pressure kneader for 1 to 1.5 hours
- Impurity filtration
Use a rubber filter or ordinary extruder to filter the mixed rubber products, because mechanical impurities and undispersed compounding agent particles can cause quality problems when silicone materials are used for molding, extrusion, coating, diaphragm and other processes. Meiping strictly implements each process, controls quality, and ensures customer quality from the source. The temperature of the barrel and screw is controlled to a low level, and the filter size is preferably 120~200 mesh.
- Refining
After the silicone material is placed for a period of time, the internal gel content will increase and its plasticity will decrease, so it must be refined when used. The rubber should be re-refined in moderation. If it is not re-refined enough, the rubber will have poor softness and an uneven surface. If it is re-refined excessively, the rubber surface will become sticky, which is not conducive to operation.
Solid silicone is industrially made of water glass (sodium silicate) as raw material, which is hydrolyzed in an acidic medium to form a gel, and then aged, washed, dried and other processes to form silica gel. Depending on the water content, it is a translucent or white solid. Commercially available products include irregular granular, spherical and microspherical silica gel, which are often used as catalyst carriers in fluidized bed operations.
When used as a catalyst carrier, silica gel is usually impregnated in a solution containing catalytically active components, so that the solution is absorbed into the pores of silica gel, and after drying, activation and other procedures, the active components are distributed on the surface of silica gel. The pore structure of silica gel has an important influence on the properties of the prepared supported catalyst, such as the pore volume and pore size distribution of silica gel. Conventionally, silica gel with an average pore size of less than 15-20 is called fine-pore silica gel; and silica gel with an average pore size of more than 40-50 is called coarse-pore silica gel.
However, the fine pore structure is not conducive to the diffusion of reactant molecules, but it can reduce the utilization rate of the inner surface of the catalyst, and the product molecules generated deep in the pores are not easy to escape from the pores, which is easy to cause deep side reactions. The pore structure of silica gel is related to the manufacturing method and conditions, such as gelation, aging, pH, temperature, time during washing, etc. The commercial silica gel can be expanded by pore expansion treatment. The commonly used method is to place it in an autoclave and add water or a salt-containing aqueous solution (such as sodium carbonate, sodium acetate) for hot pressing treatment. For example, hot pressing treatment at 320℃ and 10MPa can change the specific surface area and average pore size of silica gel from 135m2/g and 123 to 26.9m2/g and 508 respectively.
silica sol liquid silicon sol is important carrier of the material, industry usually by ion exchange method makes the silica sol sodium silicate sodium off system. It is translucent milky liquid, the content of silica in the sold goods is commonly 20% ~ 30%, and the most high is 50%, the colloidal particles diameter of 100 ~ 200 a, some items of 1300 a. A high concentration of silica sol is usually with the aid of trace amounts of sodium oxide to maintain its stability. Colloidal silica drying after into porous solids. For example, in production by oxidation of propylene ammoniation of acrylonitrile (oxygen) phosphorus molybdenum – bi – / silicon oxide catalyst, is to contain active component solution mixed with silica sol, the spray drying method into micro spherical catalyst.
The main properties of solid silicone Rubber
Excellent transparency:Solid silicone is usually milky white, and can be colored during the processing and mixing stage, suitable for a variety of color requirements.
Excellent tear strength (35N / mm):Solid silicone has good elasticity and physical strength, can remain intact when subjected to large deformations, and is not easy to break
excellent springback, yellowing resistance and heat-resistant aging
Good thermal stability and weatherability (using temperature -60 C ~ 250 C) Solid silicone performs well in a wide temperature range. It can maintain excellent physical properties, including cold resistance and heat resistance, in a temperature range of -60°C to +250°C
Physical and chemical stability: Solid silicone is a porous, polymer-structured material with high adsorption and chemical stability. It can remain stable in various chemical environments and is suitable for a variety of application scenarios
Smell
Liquid silicone rubber
Liquid silicone rubber has high transparency, no peculiar smell, and the injection molded silicone products has a glue injection port. The LSR molded silicone products is odorless.
Liquid silicone is usually odorless or has a very light odor before curing. Liquid silicone is environmentally friendly, non-toxic and odorless before curing, but masterbatch ingredients and vulcanizers are added during the curing process, and a little odor will be produced during high-temperature molding. This odor will disappear naturally after two or three days under natural ventilation and will not affect the quality of silicone products.
Solid Silicone Rubber
During the production process of solid silicone materials, some additives such as masterbatch ingredients and vulcanizers are usually added. These additives may produce some odor during the high-temperature molding process. The silicone raw material itself is non-toxic and odorless, but after adding masterbatch ingredients and vulcanizers, it will produce some odor through high-temperature molding by hydraulic presses, but this odor usually does not affect the product quality and can be eliminated by itself.
Solid silicone rubber have to use the flavor of curing agent or other curing agents, and the product has no glue injection port. With different odor according to the difference grade.
Molding process
Liquid silicone is a food-grade/Medical Grade material with high transparency and high safety. No auxiliary materials such as vulcanizing agent are added during molding, and it is sealed and fed for injection molding;
Liquid silicone is injection molding liquid silicone rubber (LSR): its full name is injection molding liquid silicone rubber, and vulcanization equipment is an injection molding machine.
The injection molding machine has a very simple process (no need for manual processes such as batching, rubber mixing, cutting, and placing in the high-temperature glue process, only one worker needs to take the product), and the product has high accuracy (all manual procedures before molding All are replaced by machines), high output (A / B glue mixed at a temperature of 130 degrees for a few seconds), many advantages such as saving labor, electricity, and materials, can produce all products produced by high-temperature glue.
LSR molding process
- LSR A + B components typically come in suitable injection molding equipment and then heat-cured into a molded rubber part. A process controlled pumping kit presses down on the buckets to force the material into static mixer and feed into the injection unit.
- Then, streams of pigment can be added and controlled. In the injection, press material will be mixed together additionally with a screw and pushed forward to create a “shot” of material, or the amount needed to fill the mold.
- After the material is injected into the mold, it will then stay clamped together to cure the LSR. Then, either an operator or a robot will remove the cured product from the mold and the cycle repeats. It is a very quick efficient process.
- Secondary steps like post bake can help reduce volatilities and improve compression set. And the deflashing process removes unwanted flashing. It’s then cleaned to remove foreign material and packaged for shipment.
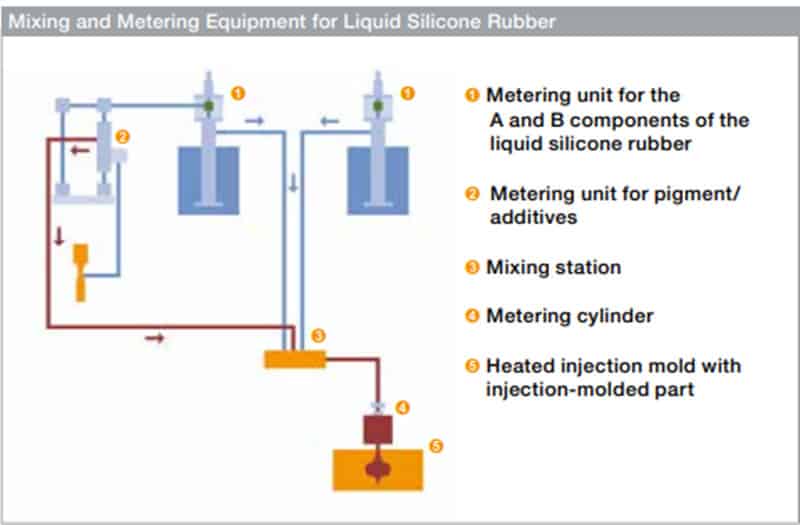
Solid Silicone Rubber compression molding
Solid silicone rubber is a transparent material, and a vulcanizing agent needs to be added during molding to speed up the vulcanization molding time. Solid silicone part is compression-molded, and after being kneaded by raw materials, it is cut into a size and thickness suitable for molding, and then placed in silicone mold, manual demolding.
The solid silicone rubber compression molding: This enables the silicone to cure once introduced to heat. To add pigment to the silicone, the silicone must be mixed using a two-mill roll. This is a labor-intensive process that has the possibility for contamination of the silicone. Once the material is pre-catalyzed and pigment is added it is weighed and often shaped to the approximate size and configuration of the desired part. It is then placed directly into the mold cavity. The rubber is then compressed between the top and bottom plates. These plates are heated to melt the silicone and vulcanize (cure) the silicone.
After the cutted silicone rubber ready the compression molding process:
1.The mold is prepared by being heated and sealed
2.Uncured Silicone (preform) is placed in the mold cavity
3.The mold is closed
4.Heat and pressure are applied (according to programmable logic controls and in accordance with temperature and pressure parameters)
5.The mold is opened and the cured rubber is removed
6.post-molding processes include deflashing, inspection, postcuring, etc.
molded silicone products mold closed Silicone mold closed Silicone mold heated Curing molded silicone products Feeding the materil on Feeding the silicone material on tooling Inspection silicone molded products
Who/Why compare Liquid Silicone Rubber/LSR and Mixed Silicone Rubber?
As R&D engineers or product engineers, we need to know the process differences between liquid silicone and compound silicone. The efficiency and precision of liquid silicone automatic injection and compound silicone manual compression molding are very different. The investment cost structure in the early, mid-term and late stages is very different: LSR equipment has high investment, but mass production dilution; HTV mold cost is low, and moderate batch is optimal. There will also be great differences. Understanding the above information clearly will help to select the most suitable materials and processing methods for the project.
As the person in charge of brand/exporter procurement/supply chain port, we need to select molds, compliance certification, and user experience requirements based on our brand and the application scenarios of our products, and select our brand and product material labels and safety material confirmations: LSR is preferred for infants/medical/electronics, and HTV is preferred for high-temperature industries/large parts. It can control costs and reduce risks.
Understanding the differences between these two materials can be based on different market demands. End users focus on precision, environmental protection, and certification, and need to meet the requirements of end customers to select silicone materials and processing technology.
As a content creator, we differentiate our company’s production process to further enhance our professionalism and win the trust of B-side customers.
When and where compare Liquid Silicone Rubber/LSR and Mixed Silicone Rubber?
Baby products, pacifiers, baby spoons, teethers, medical categories, catheters, valve bodies and other complex and precise requirements, food equipment export baking molds, straws and other high cleanliness requirements, LSR materials + Injection modling + FDA/USP VI certification are preferred
Large seals/high temperature parts, such as large gaskets, diaphragms, seals, cushion wear-resistant applications, engine gaskets, seals, industrial gaskets, thick-walled materials, barrel seals and other structural parts HTV is more cost-effective
Complex structural products, fine tolerances, high safety requirements, large-volume products, LSR process is preferred
Simple structural products, small and medium batches, cost-sensitive solutions: HTV and compression molding can be selected.
Z.S.R’s Precision Silicone mold /tooling ,Silicone Compression molding(32sets), Silicone over-molding, Liquid Silicone Rubber Injection molding: LSR molding, Liquid silicone rubber overmolding, LSR Multi-Shot (LSR/Thermoplastic/Metal), silicone Dripping molding, capabilities allow us to manufacture any type silicone rubber products for your company’s needs in an infinite variety of design, function, material, structure, shape, sizes, color, logo, pattern, package, label configurations etc. Custom silicone products manufacturing for diverse needs of worldwide—from sketch to final delivery, ensuring quality silicone products for different industry application from industrial,consumer,commercial to medical.
Contact Z.S.R to empower your silicone projects.
How much cost difference of Liquid Silicone Rubber/LSR VS Mixed Silicone Rubber?
The “genes” of silicone products begin to differentiate from raw materials:
Food-grade liquid silicone (LSR): strong fluidity, suitable for precision injection molding, raw material cost is about 45-80 yuan/kg, widely used in fields with high safety requirements such as baby pacifiers and medical devices
Solid compound silicone: through compression molding, raw material cost is about 25-40 yuan/kg, mostly used for industrial seals, mobile phone cases and other products with low transparency requirements
Beware of low-price traps: Some manufacturers use “recycled silicone” mixed with calcium carbonate. Although the quotation is as low as 15 yuan/kg, the products are prone to aging and cracking, and long-term use may lead to product recall risks.
- Process complexity: Each additional process increases the cost by 15%-30%
Silicone customization requires 12-20 processes from mold development to finished product delivery. The key cost increment links include:
Mold precision: ordinary compression molds are about 3,000-18,000 yuan, and precision liquid silicone molds require 30,000-200,000 yuan
Post-processing process: spray-on feel coating (+0.3 yuan/piece), laser engraving LOGO (+0.5 yuan/piece), multi-color layered printing (+1.2 yuan/piece)
Special performance processing: medical-grade biocompatibility certification (cost increase of 25%), flame retardant modification (cost increase of 18%)
In pursuit of “skin-like touch”, a smart watch factory added nano-coating technology to the silicone strap, and the unit cost soared by 62%, but the market premium ability increased by 3 times, verifying the value logic of “precision process investment”
- Mold cost sharing: Order volume determines the critical point of price “diving”
Molds are the largest fixed cost in the customization process, and their cost sharing directly affects the unit price:
When the order volume is 10,000 pieces, the shared cost of a set of 80,000 yuan molds is 8 yuan/piece
When the order volume increases to 100,000 pieces, the shared cost drops sharply to 0.8 yuan/piece
It is recommended that small and medium-sized enterprises adopt a “step quotation” strategy: accept a higher unit price for the first order to cover the mold cost, and expand the order volume after confirming the market response to trigger the price “diving”. A new pet product brand used this strategy to reduce the unit price of silicone massage combs from 9.8 yuan for the first order to 4.2 yuan for the follow-up order.
- Certification and compliance costs: invisible “price firewall”
Certification requirements for different application scenarios may cause the price difference of similar products to reach 200%:
Food contact grade (FDA/LFGB): testing fee is about 12,000-20,000 yuan, mainly affecting tableware and kitchenware products
Medical grade (ISO 10993): The total cost of biological testing and certification exceeds 50,000 yuan, and it is mandatory for surgical instrument accessories
National standard for children’s products (GB 6675): Physical performance test fee is about 8,000 yuan, but products that fail to meet the standards will face a fine of 10 times the sales
V. Supplier niche: Differences in pricing logic between small workshops and high-end OEMs
A Shenzhen electronics company once received quotations from three suppliers at the same time:
Home workshop: Quotation 2.8 yuan/piece (no test report, monthly production capacity <50,000 pieces)
Medium-sized OEM: Quotation 4.5 yuan/piece (providing ROHS certification, supporting customized formulas)
Japanese-funded precision manufacturing plant: Quotation 11 yuan/piece (including medical-grade clean workshops, fully automatic unmanned production lines)
When choosing, it is necessary to balance the “cost-risk-quality control” triangle: start-up brands are suitable for cooperation with medium-sized OEMs, while medical device companies must choose suppliers with GMP qualifications.
How to choose Liquid Silicone Rubber/LSR VS Mixed Silicone Rubber?
The choice between compound silicone and liquid silicone should be determined according to the specific application scenario and needs:
Comparison of processing characteristics
Liquid silicone has good fluidity and fast vulcanization, which is suitable for scenarios that require rapid molding. It can also be used in products with thin walls, complex structures, and many details. It can be efficiently produced through injection, calendering and other processes. Compound silicone needs to disperse fillers through mechanical shearing, and the processing process requires a higher temperature (above 90°C). It is suitable for mechanical processing such as molding and extrusion of products with large product ratios and thicker wall thickness.
Differences in application fields
Liquid silicone is mostly used in scenarios that require fluidity, such as casting molding, seals, etc. Medical/baby/food, the above industries require certification, compound silicone is widely used in industrial fields such as cables, electronic components, and construction that require mechanical processing, and large-scale production is achieved through molding.
Performance characteristics
Liquid silicone can fully meet food grade requirements, with high transparency and good elasticity, and is suitable for food contact products (such as baby pacifiers). Consider the fluidity and food grade safety of liquid silicone first. Compound silicone enhances mechanical properties through fillers and is suitable for wear-resistant and high-load scenarios.
Batch size: If the number of single colors exceeds 20,000 pieces, LSR is preferred; for thousands of pieces or customized models, HTV is optional.
If it is for cost control: use HTV for initial trial production/samples, and use LSR for thick production to reduce costs and increase efficiency.
How to control Liquid Silicone Rubber/LSR VS Mixed Silicone Rubber products quality?
Controlling the quality of mixed silicone and liquid silicone products requires starting from raw materials, process parameters, equipment maintenance and other aspects:
Raw material quality control
Supplier audit: Select reputable raw material suppliers and regularly evaluate their quality management system and environmental standards.
Raw material testing: Test indicators such as volatile matter (≤0.5%), hardness deviation (±2 Shore A), Mooney viscosity (4 0-60 MU), and food grade must comply with FDA/LFGB certification.
Storage management: The warehouse needs to be dry and ventilated, and the first-in-first-out principle should be implemented to prevent the raw materials from getting damp or being stored for too long.
Mixing process control: Ensure uniform mixing, vulcanization degree, high temperature stability, strict trimming, and inspection of dimensions and mechanical properties
Temperature and time: The initial temperature of the internal mixer is set to 20-25℃, the mixing time is 8-12 minutes, and the discharge temperature is ≤50℃.
Uniformity: Use high-precision equipment to ensure that the masterbatch addition error is ≤0.3%, and adjust the agitator speed and back pressure to avoid particles.
Aging treatment: After mixing, let it stand for more than 24 hours (medical grade needs to be in a 10,000-level clean room) to relax the molecular chain.
Molding and vulcanization Mold and exhaust: Clean the grease on the mold surface and set 0.5-1 exhaust grooves per square centimeter (depth 0.03-0.05 mm).
Vulcanization parameters: Use a PLC control system to monitor temperature (±2℃), pressure (8-15 MPa) and time (t90+10%) to ensure complete vulcanization. Monitor the ratio, mold temperature, vulcanization time, and bubble prevention; control the cold runner and seal
Environmental management Cleanliness: Medical-grade production requires an ISO 7 clean workshop, and ordinary production environments require regular cleaning of equipment and molds.
Equipment maintenance Regular maintenance: After the mold is turned over, the burrs and oil stains need to be removed; the vulcanization chamber needs to be cleaned and maintained, the mixer needs to be cleaned, the cold runner needs to be cleaned regularly to avoid residual materials, and the mold cooling channel needs to be unobstructed to avoid blockage that affects tolerances. Check the wear of components and ensure the accuracy of equipment operation.
Industry use
Liquid silicone rubber is generally used in baby products, kitchen products and medical products, and it can directly contact food and human body:
Solid silicone rubber is generally used in daily necessities, industrial miscellaneous parts, and auto parts.
Cost
The unit price of liquid silicone is usually higher than that of solid silicone. The production cost of liquid silicone is relatively high, mainly because its processing technology is complicated and the equipment requirements are high, so its market price is also relatively high. Specifically, the price of liquid silicone is usually nearly double that of solid silicone.
When will you choose the liquid silicone rubber?
When will you choose the Solid silicone rubber?
More FAQ about LSR VS Mixed silicone rubber
1: Are LSR products safe?
Food-grade LSRs comply with FDA/LFGB/USP VI, have no odor, and are suitable for infants and children/medical use
2: Does mixed silicone rubber have a smell or oil?
Mixed silicone rubber products contains peroxide vulcanizing agent. If the vulcanization is insufficient, it may have a slight smell or oily feeling
3: Is LSR necessarily stronger than HTV?
Not necessarily. In thick-walled and mechanical wear scenarios, HTV has better strength; LSR is stronger in terms of precision and aesthetics
4: Which one should I choose for a batch of 10,000 pieces?
If the structure is simple, HTV is preferred; if the structure is complex and the requirements are high, LSR can be considered
Conclusion
According to the above information, you can see there are much difference of the LSR (liquid sillicone rubber) and Solid silicone rubber.
You also can see the following sheet to know them more simply.
The Fumed silicone rubber can pass the FDA in Eu request = LFGB Standard.
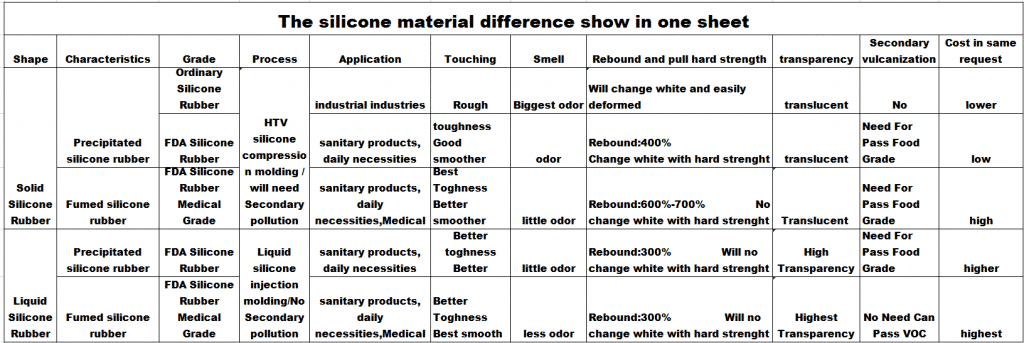
In ZSR Group has rich experience in producing Custom silicone products with LSR and solid silicone rubber. We also can help selet the right material (LSR or Solid silicone rubber) according to your project.
Z..S.R’s liquid silicone LSR molding: high automation, high precision, suitable for batch and complex products, high cost, complete certification; the best choice for food grade and baby grade.
Z.S.R’s solid silicone molding: suitable for thick-walled structural parts, low cost, less mold investment, more manual processes, suitable for small and medium batch industrial seals.
The selection should be made from the aspects of structure, batch, certification, and cost: it is recommended to quickly verify HTV in the early stage of R&D, and switch to LSR to reduce costs and increase efficiency after the batch is stable.
Any Silicone products or Silicone project need technical support, you also can custom Silicone products at ZSR Group. We will support your Silicone products from idea to life.
If you want to obtain mold quotation estimates, material manual instructions, or professional one-on-one consulting support, please feel free to contact us by [email protected], Any inquiry from you is welcome.
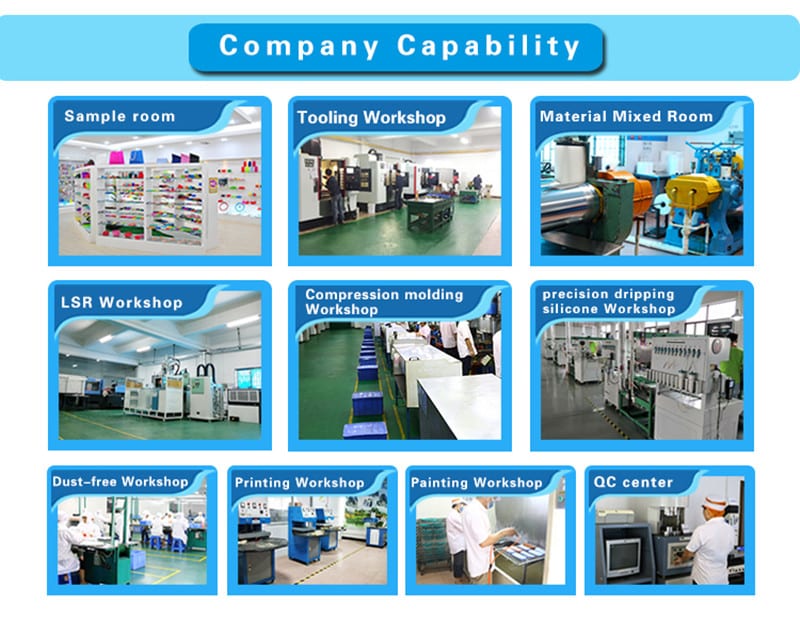
Technical Related
About Author: Z.S.R International Group
Z.S.R International Group(Hong Kong) co., Limited, is a one-stop supplier for molded silicone products and silicone products molding solution provider in the consumer products field. We offer OEM services from silicone product design to Silicone products contract manufacturing. We have the capability for custom silicone tooling, LSR(Liquid silicone Rubber) molded silicone products, solid silicone molded products, molded silicone multi-colored products. We also can custom molded silicone, custom molded LSR, custom molded dripping injection dispensing(co-injection) silicone multi-colored products.
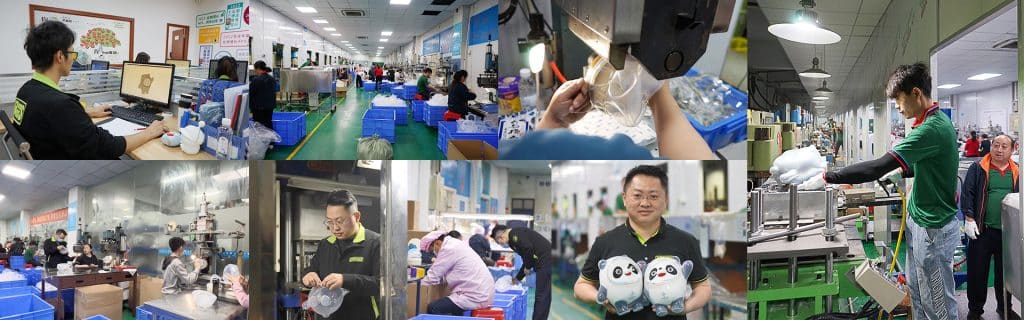