The lSR products manufacturing process
LSR products manufacturing process is a two-component liquid silicone rubber used to produce elastic items with the injection molding method.
LSR is shipped to the manufacturer in two separate containers, with an “A” compound and a “B” catalyst. Once A and B are mixed in a 1 to 1 ratio and pigment is added, the curing process begins.
Curing of the products in the mold takes place within seconds, allowing fast cycling and production of large quantities quickly.
The molder adjusts the setting on the injection molding machine to accommodate LSR and the job requirements. This includes selecting the shot size of LSR as well as temperature, pressure, cycle-time, and injection rate.
The LSR injection molding machine heats the mold and applies force on the clamp. The LSR is then delivered into the mold’s cavities. The liquid rubber silicone is cured until it solidifies. It is then ejected from the mold. The part is then finished which may include curing, inspection, deflashing, and packaging.
Multi-component LSR technology is the simultaneous injection of (LSR) in combination with engineered plastics and potentially other substrates. In what is also commonly referred to as 2K, 2shot, 2C LSR, or co-injection, it is used to develop innovative solutions, combining two or more individual materials into one fully bonded component in hard-soft and soft-soft combinations.
How do you get your LSR Injection Molded Products manufacturing process go through in ZSR Group?
Communication:
When you send your Liquid Silicone Rubber molded products requests to our company. A project engineer or sales will be assigned to your account they will work with you on every single product, from engineering assistance through full qualification/validation and approvals.
Once the products are approved and in regular production, your purchasing team can then coordinate with a customer service representative who will keep track of your product orders and deliverables. When you need to make changes to the design of a part or when you start working on next-generation product designs, that same engineer will work side-by-side with you until your product modification or new product launches successfully.
Engineering and Design:
We are here to help you during every phase of your project. Our staff provides engineering, tooling, manufacturing, quality assurance, assembly and packaging assistance. This important step helps to keep your costs low, a mission as critical to us as it is to your own organization.
Partnering with the right manufacturer early on will save you both time and money as your product goes from conception to full production.
Our Engineers can help with modifications, next-generation product enhancements and evaluation of the entire manufacturing process to determine where steps can be combined (either in your facility or ours) or even eliminated through lean cell manufacturing or advanced processing.
NDA, DFMEA & PFMEA, Mold Flow Analysis, Statistical Analysis, Color Matching.
The particular grade and manufacturer of LSR have a great impact on final product design. Often for silicones, products durometer is the dominant consideration and can range from 20 – 80 shore A.
Once the material is chosen for final product performance, many other decisions must be made regarding product shape, gating, material usage, and most importantly cost. The best method for determining these is to ask a series of questions:
How will the product be molded?
Products geometries can have a great deal of impact depending upon the type of molding used. Some work well with automation typical for horizontal LSR molding, while others work better for the manual operation of vertical machine molding. Also, the complexity of the geometry plays a role in governing the size of the mold and thus the size of the molding machine.
How will the product be demolded?
Design for ease of demolding is just as important as design for molding. Silicone has a high green tear strength: meaning that very large undercuts may be designed into a product and the parts can be stretched over them during demolding without permanent deformation.
However, does not mean that any geometry may be easily removed from the mold. Silicone’s tendency to adhere to the mold steel after molding coupled with its natural tackiness can make it quite difficult to remove thick-walled highly undercut parts. Undercuts and wall thicknesses should be carefully chosen during the design phase.
How will the material be fed to the cavities?
The use of a traditional runner system to feed material through the gate yields a great deal of waste material that cannot be reused. A cold runner system, on the other hand, allows for direct gating with no material wasted.
These systems consist of water-cooled nozzles within the mold which feed material to each cavity, allowing for direct gating and no curing of the material within the cold nozzles. This system is analogous to a hot runner system for thermoplastics molding.
Further Reading: Silicone Material
What type of gate should be used?
Once the decision has been made regarding the type of runner system, gates may be chosen. For a cold runner system, pin, submarine, or other automatic degating designs are often used. Standard runner systems may also utilize the aforementioned gate styles along with edge, fan, ring, or other gate types. Although these are the most common methods, nearly any gating style may be used with LSR as with thermoplastics.
What is the best gate location?
As with thermoplastics injection molding, cavity filling should be achieved from the thickest areas of the part. If part of an assembly, gate location should not interfere with assembly or action of the final product.
Tooling:
Product design and tooling design go hand in hand with LSR molding. Tool designers must take into account not only customer requirements of dimension and cavity geometry, but also how to reconcile those requirements with the limited space within an injection molding tool. These are some questions asked by mold designers and toolmakers:
- Wall and Rib Thicknesses
- Mass Reduction and Uniform Wall Thickness
- Parting Lines
- Undercuts
- Part Ejection
- Draft
- Gating and Venting
- Expected Tolerances
What is the linear shrinkage of the LSR?
As with thermoplastics there is an overall shrinkage of molded LSR products after cooling. In general the linear shrinkage is 2-3%, but varying geometries change this value. Additionally, shrinkage is drastically affected by processes such as overmolding, where inserts do not shrink and the curing silicone shrinks less than expected. For cases where shrinkage is unknown or uncertain for a particular geometry, prototype tooling is often used to simulate full production
How should the mold be heated?
Consistent heating of LSR molds is crucial to producing parts of proper geometry both throughout a single run and between runs. Options for heating methods include resistance or induction. Both styles may be placed inside the plates of the mold or inside a universal base that heats the entire mold from the outside only.
More precise control is given by placing heaters directly in the mold plates so that the thermocouples tied to the PID controller can more effectively change the heater on/off timing. The choice of heating type depends largely on budget and geometric considerations since heating the mold directly increases costs and heaters must be placed so that they avoid mold cavities, cores, and slide actions.
How much venting is required?
Venting is very important for proper LSR molding. LSR’s low viscosity results in very high injection speeds which tend to cause dieseling, or scorching, at the end of fill. This low viscosity also causes LSR to flash more readily than thermoplastics so the vents must not be cut as deep: near 0.005 mm (0.0002 in) for LSR compared to 0.025 mm (0.001 in) for thermoplastics. In addition to typical venting, vacuum evacuation is also common for LSRs as the trapped air can be more quickly taken from the cavity, reducing the chances of gas trapping.
What surface finish is best for proper demolding?
Surface finish is often dictated by customer requirements or product design. However, when finishes may be chosen, non-polished finishes are preferred – SPI mold finish of B1 or less. are highly polished and LSR tends to adhere to the mold surface, making demolding difficult.
What items may be improved to ease maintenance in the future?
Properly maintained molds are crucial to LSR molding. Tight tolerances are necessary to prevent flashing and dimensional issues. Wear items such as bushings and side locks which are used for alignment should be easy to change and placed on a regular PM schedule.
Cavities and cores should be easy to access for regular cleaning. If the mold has a cold runner, it should be designed so that disassembly and assembly are as simple as possible. Often, cold runner nozzle tips and shutoff needles need to be cleaned of cured material, and ease of access is of great importance to limiting downtime.
Process Considerations
Though similar to thermoplastic injection molding in many ways, LSR molding processing can be quite different.
When a high-consistency silicone is brought into our facility, it almost always needs some sort of labor to transform it into a moldable size and shape. In most cases, all that’s required is for the material to be sized and shaped for the mold cavity — which is referred to as performing the material.
Some materials have an extra step of adding cures to the material (which were left out to increase the shelf stability of the material). An LSR removes all of those steps. Here is a look at the LSR manufacturing process:
1. LSR A + B components typically come in a 5 gallon pail or 55 gallon drum. A process controlled pumping kit presses down on the buckets to force the material into static mixer and feed into the injection unit.
2. Then, streams of pigment can be added and controlled. In the injection, press material will be mixed together additionally with a screw and pushed forward to create a “shot” of material, or the amount needed to fill the mold.
3. After the material is injected into the mold, it will then stay clamped together to cure the LSR. Then, either an operator or a robot will remove the cured product from the mold and the cycle repeats. It is a very quick efficient process, that typically averages 30 seconds.
4. Conversely, with an organic material or high-consistency silicone, the average cycle time to get a part made is around six or more minutes. Peroxide-cured materials take even longer, commonly around nine minutes. LSR can lead to significant cost savings in labor over a high-consistency silicone material.
5. Secondary steps like post-bake can help reduce volatilities and improve compression set. And the deflashing process removes unwanted flashing. It’s then cleaned to remove foreign material and packaged for shipment.
Learn More About Silicone Molding Method And Process
The key components of the conventional, two-part liquid injection molding process include the following:
Supply drums: The plungers, or liquid silicone supply containers, connect to the pumping system. Many two-container setups include a third container for pigment.
Metering units: The metering device pumps the two liquid materials in predetermined ratios, which ensures a concurrent release at a steady ratio.
Mixers: Once the liquid-forming materials pass through the metering unit, a static mixer combines the materials. The blended material is pressurized and pushed into the mold.
Injectors: This device moves the LSR-forming material into the pumping mechanism under pressurized force. The machine operator has the capability to adjust the pressure, as well as the injection rate. This parameter differs according to the project specifications.
Nozzles: The liquid compound flows into the mold through a nozzle that has an automatic shut-off valve. This valve prevents the mixture from leaking or the mold from overfilling.
LSR Molding Cycle: Cure / Meter & Mix Material Eject / Brush Mold Close Needle Valve Close Pack / Hold LSR Injection Mold Open Needle Valve Open Start
In an ideal production environment, the basic liquid injection molding machine should be as lean and as compact as possible. Secondary devices should be configured to address the needs of a particular project.
Molding Parameters:
Rather than plastification during cooling, LSRs need only be conveyed through the screw flights for the next shot. As such, back pressures and screw speeds are kept low; only fast enough to complete dosing before the cure portion of the cycle is complete. Shot size is determined by the rule of thumb that 99% of the cavity should be filled.
The final filling will be done by expansion of the material during curing, so no cushion is needed. It is important not to fill the cavity completely as this is the main culprit for flashing Injection speeds should be set to optimize pressure during filling. Again, due to its low viscosity, LSR flashes easily and must be molded under as low a pressure as possible. Packing pressures are generally low due to expansion during cure. The time for complete cure depends greatly on part thickness.
Mold temperatures should be setaccording to the suggested range of the material supplier. Hotter molds will cure faster, so shorter cycles can be achieved. However, material flow during injection is easily affected by mold temperature, so it must not be so high that the material cannot flow effectively into the cavity. Part shrinkage is also dependant upon mold temperature and should be considered during R&D for new products.
Mold Preparation:
LSR tools must be carefully prepared before production. Isopropyl alcohol or other solvents are used to remove residues left from the previous molding run or during a run if the production cycle is quite long. Often, molds must be cleaned as frequently as once per week. After cleaning, mold release agents are applied to the cavities and runners, and are allowed to dry before the mold is placed into the injection molding machine.
Material Changes:
LSR materials require constant pressure during pumping and thus material containers may not be changed while the pumping unit is operating. This means that the injection molding machine must be stopped in order to remove the empty container and replace with new material.
The best method by which this situation may be avoided is via a second pumping unit which may be switched by valve in order to continually operate the molding machine. These units are quite expensive, however, so substantial capital investment is required to ensure continual operation.
Potential Innovations
Two-Shot Molding:
Typically, LSR overmolding requires the use of a priming agent to prepare the component surface for the liquid silicone. Recent advancements in self-bonding LSRs have lessened the necessity of priming, as they are designed to bond directly to a variety of materials.
This advancement has also opened the door to potential innovations such as two-shot molding, where thermoplastics and LSRs are processed on a single machine, with a single mold. This process allows for not only lowered manufacturing costs but also increased design freedom by molding the two components together.
Improved Cold Runner Technology:
Cold runner technologies are currently in a state of newfound importance. For the past few decades, each LSR manufacturer had developed proprietary cold runner shutoff nozzles and cooling technologies.
Recently, several manufacturers have introduced off the-shelf cold runner systems akin to the hot runner systems available for thermoplastic molding. Standardization may lead to improved systems which operate even more efficiently than those currently available.
Conclusion
ZSR Group has rich experience in producing Custom Molded LSR Products and silicone products molding with FDA or LFGB Approved standard. We have the FDA register list number 3011147430.
Any Custom molded Silicone products or Molded Silicone project need technical support, you could contact Z.S.R Group from our website.
Technical Related
About Author: Z.S.R International Group
Z.S.R International Group(Hong Kong) co., Limited, is a one-stop supplier for molded silicone products and silicone products molding solution provider in the consumer products field. We offer OEM services from silicone product design to Silicone products contract manufacturing. We have the capability for custom silicone tooling, LSR(Liquid silicone Rubber) molded silicone products, solid silicone molded products, molded silicone multi-colored products. We also can custom molded silicone, custom molded LSR, custom molded dripping injection dispensing(co-injection) silicone multi-colored products.
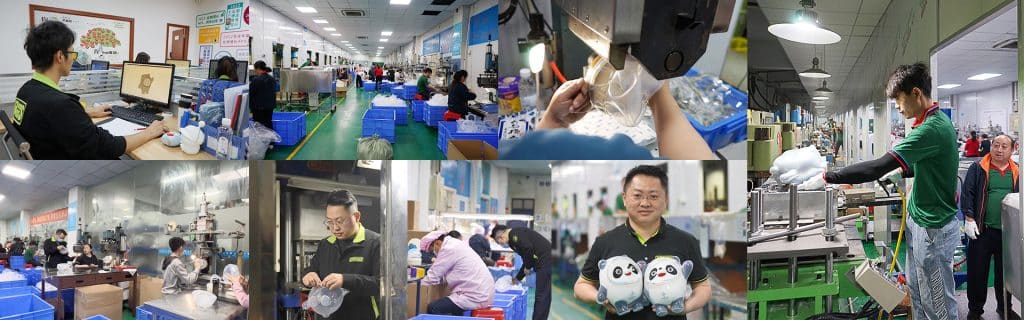