How do you make a liquid silicone rubber mold or tooling?
The good Liquid Silicone Products come from a precision liquid silicone rubber mold or tooling. How do you make a liquid silicone rubber mold or tooling? There are five key factors that go into making a high-quality Silicone injection molded part: part design, engineering, tool building, material selection and manufacturing.
Parts Design Analyze:
The process of LSR injection molding is designed to produce precision parts at a low cost. The product’s design must be developed to maximize the efficiency inherent in high-volume molding. With the right design, products can be made consistently and with quality. Without a good design, costly processing mistakes can be made.
Around the industry, most molding professionals agree that there are key design elements that must be held to a high standard for the LSRinjection process to work properly. They include wall thickness (t), rib design, boss design, corner transitions and weld lines and gate placement, and properly placed vents.
NDA, DFMEA & PFMEA, Mold Flow Analysis, Statistical Analysis, Color Matching.
The particular grade and manufacturer of LSR have a great impact on final products design. Often for silicones, products durometer is the dominant consideration and can range from 20 – 80 shore A. Once the material is chosen for final product performance, many other decisions must be made regarding products shape, gating, material usage, and most importantly cost. The best method for determining these is to ask a series of questions:
How will the product be molded?
Products geometries can have a great deal of impact depending upon the type of molding used. Some work well with automation typical for horizontal LSR molding, while others work better for the manual operation of vertical machine molding. Also, the complexity of the geometry plays a role in governing the size of the mold and thus the size of the molding machine.
How will the product be demolded?
Design for ease of demolding is just as important as design for molding. Silicone has a high green tear strength: meaning that very large undercuts may be designed into a product and the parts can be stretched over them during demolding without permanent deformation. This, however, does not mean that any geometry may be easily removed from the mold. Silicone’s tendency to adhere to the mold steel after molding coupled with its natural tackiness can make it quite difficult to remove thick-walled highly undercut parts. Undercuts and wall thicknesses should be carefully chosen during the design phase.
How will the material be fed to the cavities?
The use of a traditional runner system to feed material through the gate yields a great deal of waste material that cannot be reused. A cold runner system, on the other hand, allows for direct gating with no material wasted. These systems consist of water-cooled nozzles within the mold which feed material to each cavity, allowing for direct gating and no curing of the material within the cold nozzles. This system is analogous to a hot runner system for thermoplastics molding.
What type of gate should be used?
Once the decision has been made regarding the type of runner system, gates may be chosen. For a cold runner system, pin, submarine, or other automatic decorating designs are often used. Standard runner systems may also utilize the aforementioned gate styles along with edge, fan, ring, or other gate types. Although these are the most common methods, nearly any gating style may be used with LSR as with thermoplastics.
What is the best gate location?
As with thermoplastics injection molding, cavity filling should be achieved from the thickest areas of the part. If part of an assembly, gate location should not interfere with assembly or action of the final product.
Engineering:
Wall and Rib Thicknesses:
Mass Reduction and Uniform Wall Thickness:
Parting Lines:
Undercuts:
Part Ejection:
Angle Draft:
Gating and Venting:
Expected Tolerances:
Tooling:
Product design and tooling design go hand in hand with LSR molding. Tool designers must take into account not only customer requirements of dimension and cavity geometry, but also how to reconcile those requirements with the limited space within an injection molding tool. These are some questions asked by mold designers and toolmakers:
What is the linear shrinkage of the LSR?
As with thermoplastics, there is an overall shrinkage of molded LSR products after cooling. In general the linear shrinkage is 2-3%, but varying geometries change this value. Additionally, shrinkage is drastically affected by processes such as overmolding, where inserts do not shrink and the curing silicone shrinks less than expected. For cases where shrinkage is unknown or uncertain for a particular geometry, prototype tooling is often used to simulate full production
How should the mold be heated?
Consistent heating of LSR molds is crucial to producing parts of proper geometry both throughout a single run and between runs. Options for heating methods include resistance or induction. Both styles may be placed inside the plates of the mold or inside a universal base which heats the entire mold from the outside only. More precise control is given by placing heaters directly in the mold plates, so that the thermocouples tied to the PID controller can more effectively change the heater on/off timing. Choice of heating type depends largely on budget and geometric considerations, since heating the mold directly increases costs and heaters must be placed so that they avoid mold cavities, cores, and slide actions.
How much venting is required?
Venting is very important for proper LSR molding. LSR’s low viscosity results in very high injection speeds which tend to cause dieseling, or scorching, at the end of fill. This low viscosity also causes LSR to flash more readily than thermoplastics so the vents must not be cut as deep: near 0.005 mm (0.0002 in) for LSR compared to 0.025 mm (0.001 in) for thermoplastics. In addition to typical venting, vacuum evacuation is also common for LSRs as the trapped air can be more quickly taken from the cavity, reducing the chances of gas trapping.
What surface finish is best for proper demolding?
Surface finish is often dictated by customer requirements or product design. However, when finishes may be chosen, non-polished finishes are preferred – SPI mold finish of B1 or less. are highly polished and LSR tends to adhere to the mold surface, making demolding difficult.
What items may be improved to ease maintenance in the future?
Properly maintained molds are crucial to LSR molding. Tight tolerances are necessary to prevent flashing and dimensional issues. Wear items such as bushings and side locks which are used for alignment should be easy to change and placed on a regular PM schedule. Cavities and cores should be easy to access for regular cleaning. If the mold has a cold runner, it should be designed so that disassembly and assembly are as simple as possible. Often, cold runner nozzle tips and shutoff needles need to be cleaned of cured material, and ease of access is of great importance to limiting downtime.
Material Selection:
Temperature: Thermal stress that may occur during normal and extreme use conditions, as well as during assembly, finishing and shipping.
Chemical resistance: The effects that occur when any solid, liquid or gas come in contact with the part.
Agency approvals: Governmental and private standards for properties such as heat resistance, flammability, and electrical and mechanical capabilities.
Assembly: The Silicone cooperation with all assembly steps like bonding, mechanical fasteners and welding.
Finish: The material’s ability to produce the desired finish such as gloss, smoothness and other appearance values as it comes from the mold.
Cost: Resin pricing as well as the cost calculations for manufacturing, maintenance, assembly and disassembly to reduce labor, tooling, finishing and other costs.
Availability: The resin’s availability in regard to amount needed for production.
Conclusion:
In Z.S.R Group, Our offerings range from product and electronics design to prototyping and manufacturing. We apply our knowledge of technology to most markets, among them consumer products, baby products, outdoor products, beauty and health care products. With our entrepreneurial spirit and with our in-house tooling workshop, we believe in building products right the first time and introducing them quickly to market. For more, visit consumersiliconeproducts.com
Technical Related
About Author: Z.S.R International Group
Z.S.R International Group(Hong Kong) co., Limited, is a one-stop supplier for molded silicone products and silicone products molding solution provider in the consumer products field. We offer OEM services from silicone product design to Silicone products contract manufacturing. We have the capability for custom silicone tooling, LSR(Liquid silicone Rubber) molded silicone products, solid silicone molded products, molded silicone multi-colored products. We also can custom molded silicone, custom molded LSR, custom molded dripping injection dispensing(co-injection) silicone multi-colored products.
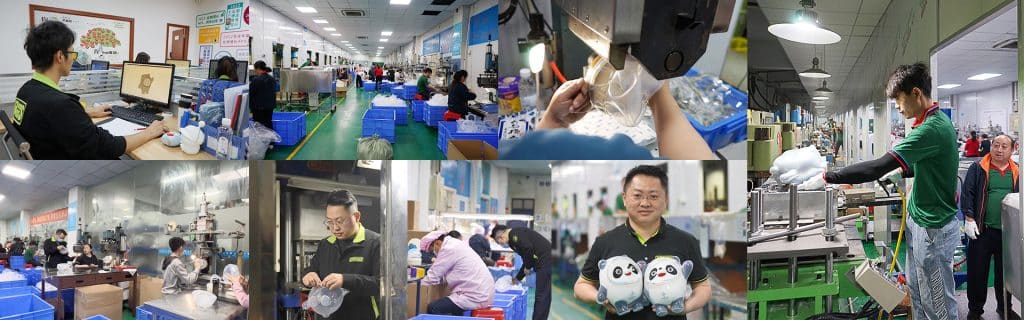