What are the 4 stages of Silicone injection Moulding?
Liquid silicone injection molding is ideal for creating detailed, temperature-resistant products from thermoset liquid silicone, either alone or with over-molding. Silicone Injection molding involves the high-pressure injection of a polymer into a mold where it is shaped.
The individual parts of this process are very short. The whole injection molding process usually lasts from 2 seconds to 2 minutes. There are four stages in the cycle. These stages are the clamping, injection, cooling and ejection stages.
What are the 4 stages of Silicone injection Moulding?
Clamping:
The mold is usually heated by water flowing inside the mold or by electrical heaters. Additionally, a cold runner system can be used to prevent the premature curing of the flowing silicone in the runners or their vicinity.
In Liquid Silicone Rubber molding area: LSR A + B components typically come in suitable injection molding equipment and are then heat-cured into a molded rubber part. A process-controlled pumping kit presses down on the buckets to force the material into the static mixer and feed it into the injection unit.
Injection:
The silicone rubber material can be pumped through pipelines and tubes to vulcanization equipment into the Liquid Silicone Rubber injection molding machine. The heat surrounding the barrel and the pressure serve to melt the pellets.
The volume of material injected is called the ‘shot’. This injection time is finished when 95%-99% of the mold is filled. The stage of injection mold pressure preservation is also a stage of continuous pressure application.
The density of Silicone also increases with the increasing pressure of the injection molding machine. In the process of injection mold pressure preservation, the cavity is slowly filled with Liquid Silicone rubber material, resulting in the injection mold back pressure gradually increasing.
In the process of pressure preservation, the screw of the injection molding machine moves forward slowly, and the rate of Silicone is relatively slow. In this case, the flow is called pressure preservation flow.
In the injection mold pressure preservation stage, the Silicone is cooled, resulting in accelerated solidification, increased melt viscosity, and large resistance in the cavity. At the later stage of pressure preservation, the material density continues to increase, and the Silicone products are also molded by injection molding. When the gate solidifies, the stage of pressure preservation is finished, and the pressure in the cavity reaches the maximum value.
Cooling:
For the Liquid Silicone Rubber injection mold, the cooling system design is very important. This is because after being released from the mold the molded silicone products only cool to certain rigidity to avoid deformation due to external force.
Since the cooling time accounts for about 70% ~ 80% of the whole molding cycle, a good cooling system can greatly shorten the molding time, improve injection production and reduce the cost.
Ejection:
Liquid Silicone Rubber Molding does not require ejector pins like the standard practice with thermoplastic molds. When designing the products, the entire product is retained on one-half of the mold when it is opened at the end of the molding cycle. Under ideal conditions, the product’s features will rise above the parting line surface, which makes the products easier to demold.
Silicone injection molding plays an important role in every field.
Learn More About Silicone Molding Method And Process
The application of silicone injection molding optimizes product performance and shortens production and processing time.
Z.S.R Group has Liquid silicone injection molding technology since 2007. Since that time, we have prototyped and molded many silicone molding products from compression molding, injection molding and epoxy molding.
We are an ISO 14001 & ISO 9001 certified company making us well qualified to be your best partner for silicone injection molding products.
Please contact our Product Specialist by Email: info@consumersiliconeproducts.com
Technical Related
About Author: Z.S.R International Group
Z.S.R International Group(Hong Kong) co., Limited, is a one-stop supplier for molded silicone products and silicone products molding solution provider in the consumer products field. We offer OEM services from silicone product design to Silicone products contract manufacturing. We have the capability for custom silicone tooling, LSR(Liquid silicone Rubber) molded silicone products, solid silicone molded products, molded silicone multi-colored products. We also can custom molded silicone, custom molded LSR, custom molded dripping injection dispensing(co-injection) silicone multi-colored products.
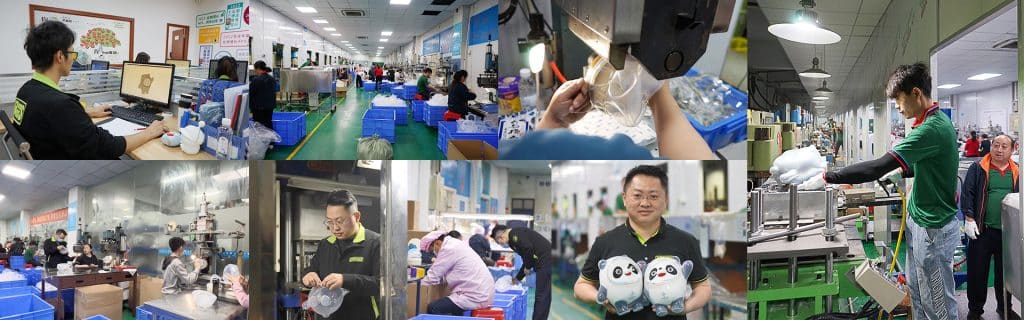