Prototype or Mass Production Molds: Which is Right for Your Silicone Product?
Clients often have questions about the difference between prototype molds and mass-production molds when creating their own silicone products. This article is dedicated to solving your questions in the silicone industry, the difference between prototype and mass production molds from the aspects of definition, application stage, advantages, etc. If you have similar questions, please read this article in depth. I hope it will solve your doubts. If you have other questions, please get in touch with our expert.
What is a silicone prototype mold?
Silicone sample mold, also known as prototype mold, is a mold made by clients to verify the sample effect or test the feasibility of the sample structure. The main function of the sample mold is to make samples in the early stage of product customization. It is usually low-cost and short time to make.
In the development process of silicone products, the role of sample molds is particularly important. When the size and structure of a new product have not been fully determined, making a sample mold for proofing and adaptation can help to understand the actual effect of the product in advance and make subsequent product size and structure adjustments, thereby avoiding unnecessary trouble caused by modifying the mold.
In addition, the sample mold can also simplify the mold modification process during the development stage, shorten the time required for mold opening and subsequent modifications, and effectively avoid the risk of mold scrapping due to excessive modifications. Copper, Steel (tool steel, carbon steel) and aluminum; Production grades range from Class S50C a prototype mold.
After confirming the size and structure of the product through the sample mold, the need for modification of the mass production mold can be reduced, ensuring the stability and quality of silicone product production.
As the cost of mass production mold is relatively high, and the cost of modification is also high (much higher than a sample mold).
So, to ensure the accuracy and compatibility of the product before mass production, it is recommended that customers create a sample mold with 1 or 2 cavities. Because this allows customers to see and confirm their own designs before mass production mold making.
Generally speaking, the prototype mold can only be used to verify the accuracy of the silicone product and cannot be used for mass production, because the material used is not necessarily high-quality steel, and the production efficiency is very low. Under normal circumstances, the sample mold can only produce 50 pieces of samples at most to complete its mission, and the sample fee is generally at least 2.5 times the cost of the MOQ bulk product.
What is silicone mass production mold?
Mass Production Mold refers to molds produced from steel material when large quantities of products are needed, which allows them to have a longer life than thousands or even millions of times on a mold. The production molds phase is where the final product is fabricated and tested. This phase is important as it sets a great ground for large-scale, mass production. As a result, this type of molds is designed for long-term use and it ensures the molds can produce silicone products to the correct specification and standards.
Silicone mass production mold refers to a mold used for mass production of silicone products. After the product design is verified, the mass production mold will be used for mass production to meet market demand. The design of the bulk mold pays more attention to production efficiency and cost control
Features of silicone mass production molds:
Application of silicone mass production molds
The bulk mold is widely used in the actual production process, especially after the product design is verified, for mass production of silicone products to meet large-scale market demand. production grades range from Class S50C a prototype mold, to Class P20, an extremely high production mold.
Usually, in order to increase production capacity and lower product unit price for clients. Z.S.R will make the mass production mold after our clients confirm the prototype samples.
Mass production mold always has several cavities (could molding several products), then samples mold only one or two cavities. Such as molding a product will take 5 minutes, if mold has 8 cavities means that 8 products could be molded in 5 minutes. If the mold only has one cavity, then only one product could be molded in 5 minutes, resulting in low capacity and a higher unit price.
When will you need the prototype mold?
When customers develop and design new products: When customers design a new silicone product, or are not sure about the size and structure of the product, they need to open a prototype mold to test whether the product’s performance and structure meet the expected use effect. If they are not ok, can modify and re-build an new ones. It can save the time and cost for the clients and better solve customer problems.
Product demand is small: For products with small demand in the early stage, you can open a sample mold for experimentation first, and then open a large mold for mass production after the demand increases
Product structure is relatively complex: For silicone products with more complex structures, making sample molds can simplify the mold modification process, reduce the time for mold opening and subsequent modifications, and reduce the risk of mold scrapping due to excessive modifications
The role and advantages of silicone sample molds include
Verify sample effect: Sample molds are used to verify sample effects or test the feasibility of sample structures to ensure that the actual effect of the product is consistent with the design
Reduce modification risks: Through sample molds, you can understand the actual effect of the product in advance and avoid unnecessary trouble and costs caused by modifying the mass production mold.As the mass production mold is high cost to modify or re-build.
Reduce costs: The cost of the sample mold is low, and even if it is scrapped, it will not cause too much loss, thus saving customers a lot of resources and costs
Ensure production stability: Once the size and structure of the product are confirmed through the sample mold, it can be directly applied in subsequent mass production, reducing the need to modify the mass production mold and ensuring production stability and quality
When will you use the mass production mold?
Silicone mass production molds can quickly and accurately replicate complex shapes and structural details to ensure the beauty and consistency of the product.
It can be mass-produced, easy to operate, and relatively low cost, which can save production costs and time costs for enterprises and improve production efficiency.
Usually, in order to increase production capacity and lower product unit price for clients. We will make the mass production mold after our clients confirm the prototype samples.
Mass production mold always has several cavities (=could molding several products, see below picture and attached video), then samples mold only one or two cavities. Such as molding a product will take 20 minutes, if mold has 8 cavities means that 8 products could be molded in 20 minutes. If the mold only has one cavity, then only one product could be molded in 20 minutes, resulting in low capacity and a higher unit price.
How to create the silicone mold?
The development and customization of silicone molds is a complex and delicate process involving multiple links and key technologies. This process begins with a deep understanding of the needs, and goes through design, manufacturing, trial molds, mass production preparation, and final product delivery.
1. Project preparation and demand analysis
The first step in the development of silicone molds is to have a deep understanding of customer needs. Customers usually need to clarify the use, size specifications, appearance requirements, performance parameters and other key information of silicone products, and may provide preliminary design sketches or samples as reference. This information is the basis for subsequent design and manufacturing.
The manufacturer conducts a detailed demand analysis based on the information provided by the customer to ensure that both parties agree on their expectations for the product. During the demand analysis phase, the project team will also evaluate the expected output of the product, material properties, etc., especially for liquid silicone over molding molds, and pay special attention to the bonding strength and sealing between silicone and embedded materials (such as metal, plastic, etc.) and the demolding performance of the mold.
In this stage, Z.S.R ‘s sales team and engineer will work with you closely to more all your thing clear and modify the design to let them fit the Manufacture.
2. Mold design
Based on the demand analysis, the design team uses CAD (computer-aided design) software to transform ideas into precise three-dimensional models. This stage includes key elements such as the overall structural design of the mold, parting surface design, gate location, and vent arrangement. The fluidity and curing characteristics of liquid silicone should be fully considered during design to ensure uniform filling and avoid bubbles.
The selection of mold materials is also crucial. According to product requirements, mold materials are mostly steel or aluminum, such as aluminum alloy, stainless steel or special alloy steel, to ensure sufficient strength and durability. These materials must have good thermal conductivity, wear resistance and corrosion resistance to adapt to the high temperature and high-pressure molding environment of liquid silicone.
In addition, the design team must also plan a reasonable cooling system to control the mold temperature, accelerate the curing process of liquid silicone, and improve production efficiency. The location and layout of the cooling water channel must be carefully planned to ensure uniform temperature in all parts of the mold. Z.S.R have expert engineer more than 10 years’ experience to ensure your silicone molds was design in great gate, parting line and others.
3. Mold manufacturing
After the mold design is completed, it enters the manufacturing stage. According to the design drawings, the mold material is precisely processed by CNC machining, electro spark machining (EDM), wire cutting and other technologies to form the various components of the mold. During the processing, the dimensional accuracy and surface roughness must be strictly controlled to ensure the sealing and durability of the mold.
Z.S.R can take a full-service model from silicone project beginning to markets. Not only are we dedicated to meeting the highest manufacturing standards possible, and we are also constantly focused on solving the unique problems that you have. With 6 sets of advanced CNC machining centers and 3 sets of EDM spark machines for mold; So, we can make most of the silicone mold and repair the silicone mold in our factory to catch up your time needed
After the processing is completed, the mold components are assembled and initially debugged. Check whether the mold opens and closes smoothly, whether the parting surface fits tightly, and whether the cooling system works properly. A small sample mold needs to be made for proofing at this stage to confirm whether the product color and hardness meet the requirements.
4. Mold trial and optimization
After assembly and debugging, the mold enters the mold trial stage. The first mold trial usually uses low-cost mold trial materials to verify the molding effect of the mold.
During the mold trial, technicians will closely observe the flow of silicone, the ease of demolding of the product, and the dimensional accuracy and appearance quality after molding.
Once any problems are found, such as bubbles, lack of material, deformation, etc., the mold needs to be adjusted immediately. The mold trial process may require multiple rounds until the mold trial product fully meets the design requirements. Through the mold trial, not only can the actual effect of the mold be verified, but also adjustments and optimizations can be made according to the mold trial results to ensure that the mold can perfectly replicate the design details.
5. Preparation before mass production
After the mold trial is successful, the mold enters the preparation stage before mass production. This includes formulating a detailed production plan, preparing production raw materials (silicone), and debugging production equipment. At the same time, a strict quality control system is established to ensure that every link meets the established quality standards.
In the preparation stage, the packaging and transportation of the product must also be considered. According to customer needs, choose appropriate packaging materials and methods to ensure that the product is not damaged during transportation. At the same time, attach necessary documents such as product manuals and certificates so that customers can understand the use and maintenance methods of the product.
Conclusion
Z.S.R consists of a strong engineering Design team; precision mold manufacturing workshops. All of silicone products manufacturing from silicone product development cycle under one roof- from designing products & building mold to launching into full-blown production. You will reduce the risks of working with multiple vendors, save your time to market & lower costs.
Are you looking for a silicone products manufacturer? Connect to work with Z.S.R Group. Please contact us today to get your design quote. From 3D CAD modeling to prototyping mold to Mass Silicone production molding, we will help you along the way!
Related Silicone Mold Article:
How to Logo or Pattern on Silicone Molds?
What is silicone over-molding
Are silicon molds the next generation of baking?
The silicone rubber injection molding process
How Does Silicone Injection Molding Work?
How do you make a liquid silicone rubber mold or tooling?
Can silicone rubber be injection molded
What is Dripping Injection Dispensing(CO-Injection) Molding?
Dripping injection dispensing(co-injection) molding Applications
What is silicone rubber compression molding?
Technical Related
About Author: Z.S.R International Group
Z.S.R International Group(Hong Kong) co., Limited, is a one-stop supplier for molded silicone products and silicone products molding solution provider in the consumer products field. We offer OEM services from silicone product design to Silicone products contract manufacturing. We have the capability for custom silicone tooling, LSR(Liquid silicone Rubber) molded silicone products, solid silicone molded products, molded silicone multi-colored products. We also can custom molded silicone, custom molded LSR, custom molded dripping injection dispensing(co-injection) silicone multi-colored products.
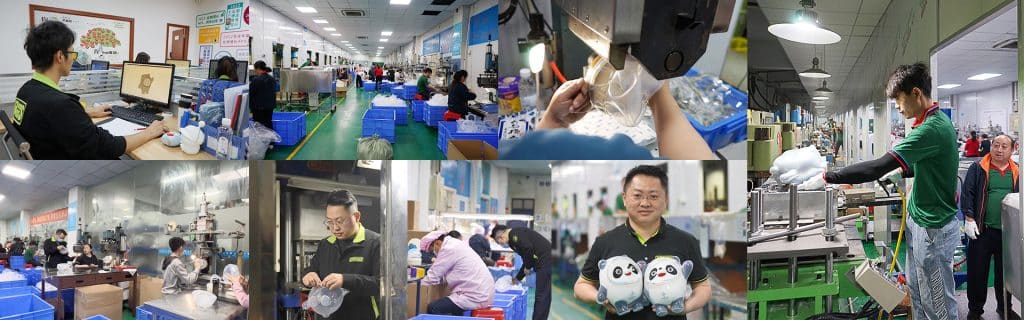