What Is Food Grade Silicone-A safe, durable and environmentally friendly new favorite in the kitchen
Food Grade Silicone
With the improvement of health and environmental awareness, consumers are particularly concerned about food contact materials. Compared with traditional plastics, food-grade silicone has become a popular material in the fields of kitchen utensils, baby products, etc. due to its advantages such as non-toxicity, high temperature resistance, antibacterial, and recyclability. This article comprehensively analyzes the nature, advantages, usage scenarios and precautions of “food-grade silicone” to help you gain a deeper understanding of silicone material.
Food-grade silicone is a high-purity silicone elastomer that complies with FDA 21 CFR 177.2600 and EU EC 1935/2004. It is usually vulcanized with a platinum system (Platinum-cured) and meets the requirements of no plasticizer, no BPA/BPS, no heavy metals and no fillers.
Free of BPA and phthalates
Non-toxic, odorless, and non-leaching at high temperatures
No risk of degradation after testing under conditions such as ethanol, acid, alkali, and hot oil
Main ingredients include:
High-purity siloxane (Polydimethylsiloxane, PDMS)
Aluminum hydroxide (for structural reinforcement)
Food-grade masterbatch (FDA certified)
Platinum catalyst (avoid the use of organic peroxides)
Safety certification: FDA, LFGB, USP Class VI, ISO 10993 (for medical use)
What is Food grade silicone made of?
Food grade silica gel is an inorganic polymer colloidal material formed by polycondensation of silicic acid. Its main component is SiO2·nH2O, which has a content of more than 98%. It is non-toxic and tasteless, and has stable chemical properties. Under normal conditions, it does not react with any acid, alkali or salt except caustic alkali and hydrofluoric acid. Since it is a colloidal structure, it has many micropores and a large specific surface area. The pore size of edible silica gel is about 8-10nm, so food grade silica gel can be used as an external desiccant for food and medicine. Since edible silica gel is refined and sterilized, it can be mixed with food and medicine according to the required amount to directly ensure the drying of food and be eaten with food, without any toxic side effects on the human body.
Where does silicone rubber com from?
Silica (Quartz): Mainly produced in China, Australia, Norway, the United States and other places.
High-purity quartz is smelted to produce metallic silicon (Si), and then undergoes chemical reactions to produce silicone oil and silicone rubber base polymers.
Major silicone rubber manufacturers in the world:
WACKER, Germany
Dow, USA
Shin-Etsu, Japan
China Bluestar New Materials, Hongda, Spark, Tianan, etc.
Product processing concentration areas:
Guangdong (Dongguan, Shenzhen), Zhejiang (Ningbo, Taizhou), Fujian (Quanzhou), China.
A small amount of customized high-end medical products in Europe.
Most of the United States is OEM or industrial product potting materials.
Food Grade Silicone Product
The main purpose of Food grade silicone is used for the manufacturing of food contact products. Food grade silicone is a type of silicone that is safe for use with foods. Silicone is used frequently in making molds to use for food that begins as liquids and solidifies. It is nontoxic; does not stain food, dishes or cookware; is easily removed from cast objects; and is safe for use on various plastic objects.
Food grade silicone is a non-toxic type of silicone that doesn’t contain any chemical fillers or by-products, making it safe for use with food.
Silicon, the naturally occurring chemical element that makes up silicone, is a metalloid, which means it has properties of both metals and non-metals and is the second most abundant element in the earth’s crust, after oxygen.
The Food Grade Silicone :
Advantages
- Highly resistant to degradation from extreme temperatures and can withstand heating and freezing without leaching off hazardous chemicals. -60℃ to 230℃ or higher, can be used for baking, steaming, freezing
- Safe and non-toxic: no BPA/BPS, no plasticizer, FDA and LFGB certified.
- Antibacterial and mildew-proof: no odor absorption, no bacteria breeding;
- Stable, Soft and tear-resistant, Durable and Flexible,not easy to age, not easy to break, a high-quality alternative to disposable plastics,suitable for repeated use.
- Hypoallergenic, odor and stain-resistant.
- Easy to clean with its smooth and soft surface.
- Does not peel or rot, making it the perfect material for eco-friendly products.
- Lightweight, easy and space-saving, therefore, can take everywhere.
- More durable than plastic and better for the environment.
- Oil-resistant, acid-resistant, alkali-resistant, corrosion-resistant, not easy to adhere to oil stains, easy to clean
- Disadvantages:
- Relatively high cost: high-purity raw materials and platinum vulcanization systems are expensive;
- Low thermal conductivity: baking utensils are prone to deformation without steel mesh support;
- Material selection varies greatly: products containing fillers or irregular coloring may compromise safety
More About Food Grade Silicone
Who care the Products in Food grade silicone ?
Housewives/healthy kitchen user: have a strong demand for non-toxic materials;
Young parents: care about the safety of baby products;
Baking experts/life users: pay attention to the user experience;
Green life advocates: pursue reusable and recyclable materials.
Who is used the Food grade silicone?
Maternal and infant brands: such as Munchkin and Beaba, widely used in pacifiers, teethers, and supplementary feeding utensils
Kitchenware brands: such as OXO and Joseph Joseph, used in cake molds, shovels, and folding bowls
Medical device companies: used for infant breathing tubes and feeding utensils
B-B customer groups: Food and maternal and infant industry buyers in Europe, the United States, the Middle East, Japan, and South Korea
When is the Food Grade Silicone critical time to use it?
Regulations require food contact safety standards (such as exports to the United States, Canada, and Europe)
Products are used in high-frequency, long-term contact with food, oils, acids, alkalis, etc for baking, steaming, freezing storage & preservation;
When the customer’s brand is positioned as high-end health, environmental protection, and maternal and child safety,Baby early complementary food and chewing toys;
Filling hot soup, heating drinks in high temperature.
Daily cleaning and weather-resistant replacement needs in the kitchen.
How to choose and test food grade silicone?
Check the packaging label “FDA/LFGB food-grade”, “platinum vulcanized”, “no discoloration”;
Purity verification: if the twisted surface does not discolor, it is usually pure silicone
How much of the Food Grade silicone rubber products?
The material price is about 30%-60% higher than ordinary silicone
FDA certification testing fee: 2000-8000 US dollars
Platinum silicone kitchenware set: $15–50;
Baby products: $8–25;
Industrial seals: $5–30/piece;
How to choose the high-quality silicone food grade products?
Prefer platinum vulcanized, no filler, no odor;
Prefer food certification, test reports and brand background;
Focus on mid-to-high-end manufacturers that provide after-sales commitments and replacement services.
The Standard of Food-Grade Silicone in different Countries
The silicone molecule is comprised of silicon, oxygen and quartz, a durable, hard, inflexible “rock”, which is the most common component of sand. Due to its resiliency, non-porous surface and sustainability, food-grade silicone is essentially soft glass
In the USA: Most countries have their own FDA standard, but the USA FDA is the most internationally applied. while FDA (Food and Drug Administration) is the base level standard in the USA and Australia. Food-grade silicone rubber is highly versatile and resistant to extreme temperatures, making it an excellent choice for products used in everything from the home kitchen to industrial manufacturing and processing plants. FDA-approved food-grade silicone is available for applications that require it, or for any usage where supreme resistance to chemical and bacterial contamination is desired.
A good material for products requiring airtight or water-tight features.
Many authorities, researchers and experts consider it to be safe for food and drink. According to Health Canada, “There are no known health hazards associated with use of silicone cookware. Silicone rubber does not react with food or beverages, or produce any hazardous fumes.”
In Europe: LFGB is standard mainly for Europe.LFGB Silicone is a premium grade of silicone that has passed LFGB testing standards.
There are two testing standards for Silicone that can be sold that are considered food grade.
Silicone products that pass either one of these tests are deemed safe for human use. In terms of pricing, products in LFGB standard will be more expensive than FDA standards, so FDA is more widely used.
The difference between LFGB and FDA lies in the different methods of testing, with LFGB testing regulations the toughest of all standards where the silicone material must pass more intensive testing compared to FDA silicone testing.
Even though both FDA & LFGB-approved silicone is considered food safe, silicone that has passed LFGB testing is higher quality silicone.
what is food grade silicone used for?
FDA food-grade silicone Food grade silicone is widely used in products that come into direct contact with food due to its excellent safety and durability is used for a wide number of purposes within the food sector including:
other food grade Silicone Products
Gaskets for food processing machinery
Food transfer tubing
Dairy tubing and fluid handling
Vending tubing
Brewery tubing and seals
Antimicrobial belting
Commercial oven seals
Coffee machine tubing
Food grade beverage gaskets
O-rings
Vibration pads
Electrical insulators
Food-grade silicone products refer to products made of silicone materials that meet national food safety standards and can be used for direct contact with food. Such products do not add any substances harmful to the human body during the manufacturing process to ensure that the products will not contaminate food under normal use conditions.
Food grade silicone products making requirements
Silicone material requirements
Silicone raw materials must meet food-grade safety standards and have good stability and reliability. Europe meets LFGB standards and other countries meet FDA standards. Ensure that the silicone products meet the safety requirements of the food grade.
silicone materials must be strictly screened and quality inspected to ensure that no unqualified raw materials are used.
Production process requirements
The production workshop must meet the hygiene standards of food industry production to ensure that the production process will not cause pollution to the product.
The production process must be strictly standardized and controlled to ensure that the silicone products produced meet the safety standards of the food industry.
The production process must adopt appropriate sterilization and sterilization measures to ensure the hygiene and safety of the product.
Quality inspection requirements
Each batch of silicone products must undergo strict quality inspection to ensure the quality and safety of the product.
Quality inspection requirements include appearance inspection, physical performance testing, chemical composition analysis and other aspects to ensure that the product meets relevant national standards.
The quality inspection results must meet relevant national standards and the company’s own quality requirements, otherwise the product will be eliminated.
How to control quality off food grade silicone products?
Material inspection: ensure that the raw materials are FDA/LFGB/ISO certified;
Process monitoring: strictly control the vulcanization temperature and time to eliminate residual platinum or decomposition products;
Factory test: heat resistance, tensile, migration limit test;
Regularly visit users for feedback and continuous optimization.
Environmental protection requirements
Silica gel production must comply with national environmental protection requirements to ensure that production does not cause pollution to the environment1.
Wastewater, waste gas, waste residue, etc. generated during the production process must be quality inspected and treated to ensure that emissions comply with relevant national standards.
How to put your logo on the food grade silicone products?
Put a logo or pattern on your food grade silicone products is a great way to give your brand a professional look and feel. With the right tools and techniques, you can easily print your logo on to your food grade silicone products with high-quality results. We hope that our guide has helped you understand how to print a logo or pattern on silicone products so that you can create stunning products for your business.
How Put Logo Or Pattern On Silicone Rubber Products?
How To Print On Silicone Products?
So if you need custom molded silicone products with company logos for your business or elevate your business with custom company logo on your food grade silicone products as promotional gifts, Connect with ZSR Today to Enhance Your Brand’s Visibility with Custom silicone products.
How to clean the food grade silicone products?
Cleaning: use neutral detergent and warm water to rinse, no rinsing is required;
Disinfection: can be steamed at high temperature, steam sterilized or dishwasher top;
Storage: cool and dry place, avoid direct sunlight.
Food Grade Silicone Products Develop suggestions
Strengthen the supply of platinum vulcanized and filler-free materials: ensure high purity;
Introduce a baking mold series with steel mesh support;
Optimize structural design: easy to clean, non-slip, and mildew-proof;
Provide high-end accessories and disinfection products for infants and children.
More FAQ for Silicone Food Grade
Q1: What is the difference between food grade and medical grade silicone?
A: Medical grade (such as USP Class VI, ISO 10993) has higher requirements and is suitable for implantation and subcutaneous use, while food grade meets food safety.
Q2: Platinum vs. peroxide vulcanized silicone, which one is better?
A: Platinum vulcanization products are stable and have no by-products; peroxide vulcanization requires post-solidification treatment and has high risks.
Q3: Will silicone products release microplastics?
A: Regular food-grade silicone has a stable structure and does not produce microplastics, but inferior coloring or fillers may be risky.
Q4: What is the highest temperature it can withstand?
A: Usually up to 230°C, and some high-end products can reach 250°C.
Q5: How to keep it odor-free for a long time?
A: Thoroughly clean + high-temperature disinfection after use, avoid oil accumulation, and dry it regularly.
Conclusion:
Food-grade silicone has gradually replaced plastics and ordinary rubber with its safety, durability, and environmental protection characteristics, and has become an important material for kitchen, baby and daily necessities. Choosing high-quality products that are platinum-vulcanized, filler-free, and certified by FDA/LFGB not only meets users’ needs for health and personalization, but also conforms to environmental protection trends. By optimizing structural design, strengthening social media marketing and high-quality after-sales service, brands can enhance market trust and user loyalty and achieve sustainable growth.
In Z.S.R group, the silicone products for babies, home and houseware, beauty and personal care, pets, outdoor and sports, protective cases and promotional gifts are all made with Food-Grade Silicone.
Any Molded Silicone products or custom Silicone products molding project needs technical support, you could buy any custom-molded Silicone products at ZSR Group. ZSR Group has rich experience in producing Food Grade Silicone products with FDA or LFGB-approved standards. We have the FDA register list number 3011147430. Contact us or email us for more information.
Technical Related
About Author: Z.S.R International Group
Z.S.R International Group(Hong Kong) co., Limited, is a one-stop supplier for molded silicone products and silicone products molding solution provider in the consumer products field. We offer OEM services from silicone product design to Silicone products contract manufacturing. We have the capability for custom silicone tooling, LSR(Liquid silicone Rubber) molded silicone products, solid silicone molded products, molded silicone multi-colored products. We also can custom molded silicone, custom molded LSR, custom molded dripping injection dispensing(co-injection) silicone multi-colored products.
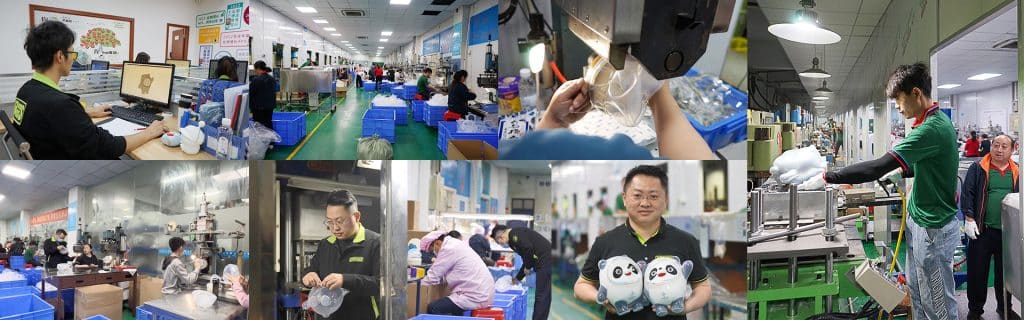