How Does Silicone Injection Molding Work?
The Application of Liquid Silicone Rubber Molding
Liquid Silicone Rubber (LSR) molding is the process used to create robust, pliable, high-precision, high-quality products in large numbers.
Liquid Silicone Injection Molding produces parts that are highly water-repellent and resistant. As such, coupled with the precise nature of their sizing, they’re ideal for a variety of other medical, commercial and domestic applications.
Liquid injection molding, or LIM, is a production process commonly used to make silicone products or to make products that need to withstand extreme conditions, regardless of the industry. The process is an injection molding process at the heart, meaning that materials are injected into a pre-made mold, where they’re then left to sit and curate. Then, the process repeats itself until the part run is complete.
Liquid Silicone Rubber injection molding has thousands of applications across a variety of industries, including medical, automotive, infant care, general industrial markets, aerospace, electronics, and many other specialized industries. While liquid silicone rubber injection molding works best for short- and long-run part production, customers can employ the process in the final stages of mass production.
Learn More About Silicone Molding Method And Process
How is the Liquid Silicone Rubber tooling making?
The LSR molding tool is fabricated using CNC machining to create a high-temperature tool built to withstand the LSR molding process. After milling, the tool is polished by hand to customer specifications, which allows six standard surface finish options.
The LSR injection tooling is loaded into an advanced LSR-specific injection-molding press, which is designed for precise control of the shot size and enables the consistent fabrication of liquid silicone rubber products.
From there, the finished LSR tooling is loaded into an advanced LSR-specific injection molding press that is precision geared for accurate control of shot size to produce the most consistent LSR parts.
At ZSR group, LSR parts are manually removed from the mold, as injector pins can impact part quality. LSR materials include standard silicone and specific grades to fit various part applications and industries like medical, automotive, and lighting. Since LSR is a thermosetting polymer, its molded state is permanent—once it is set, it can’t be melted again like a thermoplastic. When the run is complete, parts (or the initial sample run) are boxed and shipped shortly thereafter.
What are the steps of the liquid silicone rubber injection molding process?
Silicone LIM (Liquid Silicone Rubber Injection Molding) is a complex manufacturing process that relies on a lot of different variables for part runs to be successful. For instance, important components of liquid injection molding machines include:
Injectors: These devices pressurize the liquid material and maintain the two components at a homogenous temperature.
Metering Units: In order for LIM to be successful, there needs to be a catalyst and a base forming silicone material. Metering units help ensure that these two materials maintain a constant ratio while they’re in the process of being released.
Supply Drums: These components, which are also commonly referred to as “plungers,” are mixing containers.
Mixers: These combine the materials before they’re injected into the designated mold.
Nozzle: Paired specifically to a mold, these enhance injection.
Mold Clamp: This is what secures the mold during the production process, as well as what opens the mold back up when the process is completed.
Here are the primary steps involved in the liquid silicone rubber injection molding process:
The uncured liquid silicone starts in two containers, Compound A and Compound B, which connect to the pumping system. Barrel A holds the base-forming material, and Barrel B contains a catalyst. A metering unit automatically releases the two substances at a constant one-to-one ratio, as well as any pigmentation additive.
The molder can program and customize the automated injection-molding machine and have the injection setting deliver the appropriate shot size for each job. The platens and pistons, which align and close the mold, have settings for the temperature, pressure, injection rate, and cycle time-adjusted in accordance with the customer’s specifications
After the completion of the setup, the molding machine heats the mold to the appropriate temperature and applies the appropriate clamping force. The mold closes in coordination with the machine’s injector, pump, and supply. The injection mechanism then pushes the material into the mold and cavities.
A combination of heat and pressure applied to the liquid silicone rubber cures the material until it solidifies. Upon completion of the cycle, the mold opens, and the part and flashing can be removed automatically or by a worker. Then, the mold closes and repeats the process.
After the removal of the item from the mold, the post-molding process may include de-flashing, post-curing, inspection, and packaging
Learn More About Silicone Molding Method And Process
Advantages of liquid silicone injection molding
- Batches stability (ready-to-use material)
- Process repeatability
- Direct injection (no waste)
- Short cycle time
- Flashless technology (no burrs)
- Automated process
- Automated demolding systems
How Many Silicone Injection molding Z.S.R Group have:
Liquid silicone rubber molding. It is only Silicone single-color rubber molding.
LSR over-molding with other materials (Silicone, Metal, plastic, etc)
Silicone Over Silicone-First a silicone substrate is molded. Then another silicone is molded onto or around the substrate. The silicone could differ in color and/or hardness.
Silicone Over Plastic – First a rigid plastic substrate is molded. Then a soft Silicone is molded onto or around the substrate. This is often used to give a soft grip area to a rigid part.
Silicone Over Metal-First a metal substrate is machined, cast or formed. Then, the substrate is inserted into a liquid silicone molding tool and the silicone is molded onto or around the metal. This is often used to capture metal components in a silicone part.
Contact ZSR group for your silicone Products:
It’s important to select a manufacturer who understands which technique best suits your silicone products, as that should be the deciding factor. Regardless of which one is better suited, ZSR group has the capabilities to cover all your silicone compression molding, LSR injection molding and co-injection Dripping molding needs.
Technical Related
About Author: Z.S.R International Group
Z.S.R International Group(Hong Kong) co., Limited, is a one-stop supplier for molded silicone products and silicone products molding solution provider in the consumer products field. We offer OEM services from silicone product design to Silicone products contract manufacturing. We have the capability for custom silicone tooling, LSR(Liquid silicone Rubber) molded silicone products, solid silicone molded products, molded silicone multi-colored products. We also can custom molded silicone, custom molded LSR, custom molded dripping injection dispensing(co-injection) silicone multi-colored products.
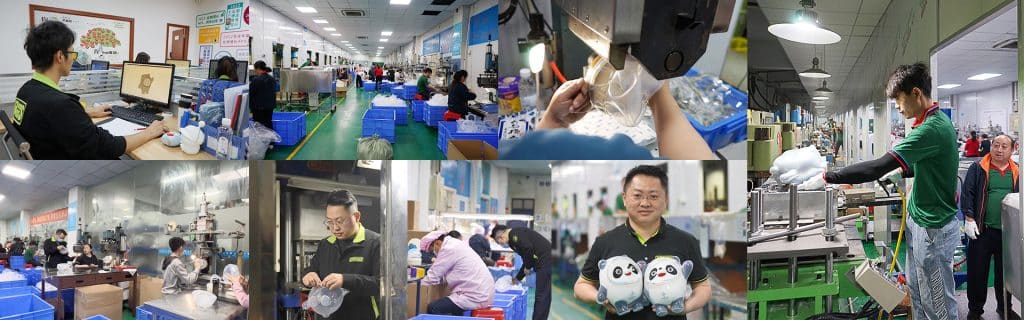