What Is The Difference Between Injection Molding And Silicone Compression Molding?
Silicone products are widely used in the fields of medical, automotive, maternal and child care, kitchenware, etc. Faced with the two mainstream molding methods of injection molding and compression molding, engineers, purchasers and brand decision makers are often confused: how to choose?
This guide will analyze the advantages and disadvantages of the two from the perspectives of cost, performance, process and market, to help you accurately locate the application scenarios and improve product competitiveness.Many Silicone products are developed through a process known as Silicone molding. Do you want to know more about the difference between injection molding and compression molding techniques?
We will focus on the differences between silicone injection molding and silicone compression molding, how these techniques work and the main advantages and disadvantages of these techniques.
ZSR Group has the ability to produce silicone consumer products to scale by silicone injection molding and compression molding.
Learn More About Silicone Molding Method And Process
1. What is injection molding?
Injection molding is a manufacturing process that allows for parts to be produced in large volumes. This process involves injecting materials into a closed mold. The LSR material is injected into the mold, quickly filled by high pressure, cooled and molded, one-time molding with high precision It is typically used as a mass production process to manufacture thousands of identical items. Injection molding materials include metals, glasses, elastomers and polymers.
An injection molding machine uses terms polymers that are heated up and injected into a mold.
It’s a cost-effective way to mass-produce a silicone or plastic product. It involves the creation of an aluminum or steel tooling, also called a mold, that is inserted into an injection molding machine. The mold has two halves, called a core and a cavity, respectively. The machines exert enormous pressure on these halves to bring them together. Thermoplastic or silicone is then melted and injected into the mold through its gates. The mold can be cooled, or tempered to a certain temperature.
In a Liquid Silicone Rubber molding, you have a “piston”, not a screw, that injects a “cold” silicone material into a very hot mold with very high pressure.
2. How does Liquid Silicone Rubber injection molding work?
Liquid silicone injection molding:
Silicone injection molding works by feeding the desired material into a heated barrel; where it is mixed and forced into a mold cavity where it cures and hardens into a specific shape. Molds are usually made from steel or aluminum and are often the most efficient way to mold silicone.
The next stage of injection molding is to create the mold itself. Most molds are made from metal, usually aluminum or steel, and precision machined to match the features of the product they are to produce.
The mold needs to be high-precision and is usually made of steel, which is expensive.
The mold design is complex and needs to consider the flow channel, exhaust and other systems.
Once the mold has been created by the mold-maker, the material for the part is fed into a heated barrel and mixed using a helical-shaped screw. Heating bands melt the material in the barrel and the molten metal or molten silicone material is then fed into the mold cavity where it cools and hardens, matching the shape of the mold. The cooling time can be reduced through the use of cooling lines that circulate water or oil from an external temperature controller. Mold tools are mounted on plate molds, which open once the material has solidified so that ejector pins can eject the part from the mold.
- The raw material is liquid and divided into two components, A and B, which are usually mixed in a ratio of 1:1.
- After mixing, it is processed by injection molding machine.
Separate materials can be combined in one part in a type of injection molding called a two-shot mold. This technique can be used to add a soft touch to plastic products, add colors to a part or produce items with different performance characteristics.
The injection molding process is adopted, and the equipment is a liquid silicone injection molding machine.
- The process is highly automated, and no manual batching, material placement and other steps are required.
- Fast molding speed and high production efficiency.
Inject the heated silicone into the cavity between the upper and lower molds through the nozzle to ensure complete filling and avoid bubbles.
Maintain a constant temperature environment for a certain period of time to allow the silicone to solidify.
After the silicone is completely solidified, separate the upper and lower molds and take out the finished product.
Further Reading: What is plastic injection molding
Molds can be made of single or multiple cavities. Multiple cavity molds can have identical parts in each cavity or can be unique to create parts of different geometries. Aluminum molds are not best suited to high volume production of parts with narrow dimensional tolerances since they have inferior mechanical properties and can be prone to wear, deformation and damage due to the injection and clamping forces. While steel molds are more durable they are also more expensive than aluminum molds.
The injection molding process requires careful design, including the shape and features of the part, the materials for the part and the mold and the properties of the molding machine.
3. What are the advantages and disadvantages of Silicone injection molding?
Silicone Injection molding comes with its own unique set of advantages and disadvantages. Here are the main advantages and disadvantages of Silicone injection molding techniques.
Advantages of injection molding
Disadvantages of injection molding
4. What is compression molding?
Compression molding is a tried-and-true method of manufacturing simple silicone rubber parts. It is a simple, high-pressure situation where vulcanized silicone rubber is transformed into a strong, useful rubber part. that’s added to an open mold. Place the preheated silicone raw material into an open mold and pressurize to cure. Suitable for large parts and simple products.The mold is closed and placed under great heat and pressure. The pressures on the top plate force the casting material to fill all mold areas and dispel air. Heat and pressure are held until the material is cured. After the parts have been cured, the silicone products are removed from the mold.
Compression molding is ideal for applications where the durometer is low and tolerances tight – and where the cost of injection molding is an issue. With over more than 10 years of experience, we have the expertise to create fairly intricate parts using compression molding.
5. How does compression molding work?
Compression molding works by combining heat and pressure to mold Silicone rubber into a shape.
Once all of the above elements are in place, vulcanized Silicone rubber is subject to compression on prepared molds.
Here are the steps of the Silicone rubber compression molding process:
- The mold is prepared by being heated and sealed.
- Uncured rubber (preform) is placed in the mold cavity- it is prepared to be formed, or molded. Every mold will have a different shape and size preform that works best. When the optimal preform has been determined, it is important to have a tolerance on both its size and shape to ensure the part forms correctly. Too much material is wasteful and can cause the flash to become too thick, while too little material can cause voids in the part.
- The mold is closed-Heat and pressure is applied in a compression molding press. Presses used in production utilize a programmable logic controller to monitor and control critical parameters like temperature, pressure and time to ensure molding takes place within a prescribed tolerance window.
- Heat and pressure are applied (according to programmable logic controls and in accordance with temperature and pressure parameters) with the mold closed.
- The mold is opened and the cured Silicone rubber is removed along with its flash.
- The silicone rubber products are then moved through the manufacturing operation to undergo Post-molding processes including deflashing, inspection, post-curing, etc.
6. What are the advantages and disadvantages of Silicone compression molding?
Compression molding is a popular technique for gaskets, seals, and grommets but isn’t the right choice for all modeling processes because its advantages and disadvantages.
Advantages of compression molding
Disadvantages of compression molding
7. Silicone Injection molding VS Compression molding
ZSR Group has the knowledge and expertise to help you understand which silicone manufacturing process is best suited to your needs. They explain that the choice between rubber compression molding or injection molding largely boils down to cost, volume and time pressures. Compression molding and injection molding each have their advantages and disadvantages, but who reigns supreme depends on what you’re producing.
It’s important to select a manufacturer who understands which technique best suits your part, as that should be the deciding factor. Regardless of which one is better suited, ZSR Group has the capabilities to cover both your compression and injection molding needs.
“Whilst neither technique is better than the other, the choice between injection or compression molding relies heavily on the requirements of your product and its application”.
Who care the Injection molding VS Compression molding?
The products Engineers/Designers becasue they are focus on product structure, precision, and physical properties.
Purchasers/Cost Controllers because they responsible Measure mold cost and life cycle cost.
Brands/Channel Dealers as they need to ensure delivery and stable supply.
Where will you use the injection molding?
Injection molding is used to efficiently and accurately replicate complex shapes such as medical devices, electronic seals, precision buttons, and maternal and infant pacifiers.
Where will you use the compression molding?
Large silicone pads, thermal insulation pads, automotive seals, professional gaskets and other application scenarios where the precision and cleanliness requirements are not so high, use silicone compression molding.
How to choice the right process? injection molding VS compression molding?
Grasp the four key words of monthly output, size, precision and material.
Injection molding for complex products with large thickness changes and internal ribs; high precision requirements: injection molding is suitable for making silicone products with high precision requirements, such as sealing rings, rubber sleeves, protective shells, etc. High automation requirements, high batches, complex structures (such as medical parts for baby pacifiers)
Small and medium batches, large-size flat parts: choose compression molding; trial production, rapid sample verification: compression molding has low cost; Limitations Low efficiency: Compared with injection molding, compression molding has a longer production cycle and is not suitable for large-scale rapid production. Size restrictions: mold shrinkage margins need to be reserved, which may affect the dimensional accuracy of the final product.
The two methods can be mixed or used in stages during the trial production phase;
If the market changes rapidly, flexible process compression or mold investment in stages is preferred.
How much of the cost of Injection molding VS compression molding?
Injection mold cost: hundreds of thousands of RMB, but long life (hundreds of thousands of times);
Compression mold cost: tens of thousands to hundreds of thousands, suitable for medium and low quantities;
Long-term operation: large-scale injection molding has a low average unit price; small and medium-sized batch compression is more economical.
How to control silicone injection molding products quality?
The quality control of silicone injection molding products requires refined management from multiple aspects such as raw materials, process parameters, mold design and production environment. The following are the key control points:
Raw material management
Supplier audit: Select silicone raw material suppliers that have passed ISO certification and have a quality management system, and regularly evaluate their supply quality and stability.
Incoming inspection: Test the volatile matter (≤0.5%), hardness (±2 Shore A), Mooney viscosity (40-60 MU) and other indicators of the raw materials. Food grade must comply with FDA/LFGB certification.
Storage: Keep away from light and dry, and implement the first-in-first-out principle to prevent the raw materials from getting wet or performance degradation.
Process parameter control Temperature setting: The mold temperature is adjusted according to the type of silicone (solid silicone 160-180℃, liquid silicone 170-210℃), and the PLC system is used to monitor the accuracy of ±2℃ in real time.
Injection speed: The injection rate of liquid silicone is controlled at 15-25 g/s to avoid turbulence and bubbles.
Pressure and time: Injection pressure is 8-15 MPa, and the vulcanization time is controlled based on the principle of t90+10%. Industrial products require secondary vulcanization (200℃×4 hours).
Mold design and maintenance Exhaust design: Set 0.5-1 exhaust grooves (depth 0.03-0.05 mm) per square centimeter to prevent bubbles from remaining.
Mold maintenance: Regularly calibrate the dimensional accuracy, and clean the residual silicone in time after use to avoid scratches affecting the molding accuracy.
Production environment and post-processing Cleanliness: Medical-grade production requires mixing and vulcanization in a 10,000-level clean room to avoid microbial contamination.
Vulcanization post-processing: The product needs to be left to mature for more than 24 hours, and the medical grade needs to be completed in a constant temperature room to ensure the relaxation of the molecular chain.
Quality inspection Online monitoring: Use sensors to monitor parameters such as size and temperature in real time, and automatically alarm when abnormal.
Finished product inspection: random inspection of product dimensional accuracy, appearance smoothness and bonding strength; medical grade products must pass biocompatibility testing.
How to control silicone compression molding products quality?
The quality control of silicone hot pressing molding products needs to start from raw materials, mold design, process parameters and environmental management:
Raw material control
Raw material pretreatment: It is necessary to test indicators such as volatile matter (≤0.5%), hardness deviation (±2 Shore A), Mooney viscosity (4 0-6 0 MU), etc. The industrial grade needs additional testing of oil resistance (ASTM D471 standard) and tear strength (≥25 kN/m).
Mold design
Precision requirements: The mold temperature needs to be set according to the material type (solid silicone 160-180℃), and the mold exhaust groove is set at 0.5-1 per square centimeter, with a depth of 0.03-0.05 mm.
Process parameters
Temperature control: The PLC system is used to track the vulcanization temperature in real time (±2℃), and medical products need to be heated in steps (120℃×1h→150℃×2h).
Pressure regulation: The pressure is controlled at 8-15 MPa during the molding process to prevent silicone overflow or uneven filling.
Time management: The curing time is adjusted according to the material thickness (t90+10%). The secondary curing of industrial products requires 4 hours of oven treatment at 200℃.
How to mantine the injection molding ? compression molding?
Injection molds need to be cleaned regularly for gates and cooling systems in case to get the pecision LSR silicone products.
Compression molds should be trimmed to reduce burrs and wear every time when one products cycle finished.
Material cleanliness should be avoided to avoid contamination that affects subsequent product quality.
More FAQ for Silicone inejction molding VS compression molding?
Is LSR injection molding suitable for large-sized parts?
- Not suitable, separate injection molding + bonding is required;
Is there a big difference in the cost of remodeling?
- Injection molding is high, costing hundreds of thousands; compression is low;
Can compression make complex structures?
- Flat structures can be made, but complex features are limited;
Is post-processing cumbersome?
- Injection molding has fewer pits that need to be repaired; compression requires burrs to be removed.
More FAQ about Compression Molding VS Injection molding
1: Is silicone injection molding more than 10,000 pieces cost-effective?
Generally, injection molding is more economical for batches exceeding 20,000 pc/color, and 10,000 pieces depends on the complexity and production cycle to choice the correct molding ways.Z.S.R Group expert can help you choose the right molding ways for you with your silicone projects.
2: Can Compression Molding only make simple shapes?
It performs poorly for complex deep cavity structures, but a certain degree of complexity can be achieved through multi-segment molds or inserts
3: Which method is more suitable for medical/maternal and infant grade products?
Medical grade requires injection molding (LSR), which has aseptic manufacturing capabilities and clean and non-toxic properties.
4: Which one is more energy-consuming, Compression Molding or injection molding?
The injection moldingmachines have high power and high mold preheating system energy consumption; The Compression Molding equipment has low power consumption, but high labor costs.
8. Conclusion
Injection molding and compression molding each have their own advantages and application boundaries:
Injection molding is suitable for high-end silicone parts with high volume, complexity and high hygiene requirements;
Compression is suitable for low volume, large and simple structure requirements.
Ultimately, the process selection should be based on the product structure characteristics, batch size, material properties and cost control. Once correctly positioned, it can significantly improve product quality, reduce operating costs, and provide solid support for the brand in market positioning and resource allocation.
In Z.S.R Group have the capability for produce silicone toolings, produce HTV Silicone products, LSR molded silicone products, Molded multi-colored Silicone products. We also can Custom silicone toolings,Custom silicone molding,Custom Silicone compression molding, Custom LSR Injection molding, Custom silicone Dripping injection dispensing (co-injection) , Custom silicone fabric coating and curing molding.We will recommend the correct molding methods according to your silicone projects needs.
If you want to obtain silicone sample evaluation, mold design consultation, process flow SOP, or need OEM, OEM silicone product solutions, please feel free to contact us!
Any Silicone products or Silicone project need technical support, you also can custom Silicone products at ZSR Group. We will support your Silicone products from idea to life.
If you like the article or you need more information from us, please leave a message or contact us by info@consumersiliconeproducts.com, Any inquiry from you is welcome.
Reach out if you have a project that needs our expertise and supply chain solutions!
Technical Related
About Author: Z.S.R International Group
Z.S.R International Group(Hong Kong) co., Limited, is a one-stop supplier for molded silicone products and silicone products molding solution provider in the consumer products field. We offer OEM services from silicone product design to Silicone products contract manufacturing. We have the capability for custom silicone tooling, LSR(Liquid silicone Rubber) molded silicone products, solid silicone molded products, molded silicone multi-colored products. We also can custom molded silicone, custom molded LSR, custom molded dripping injection dispensing(co-injection) silicone multi-colored products.
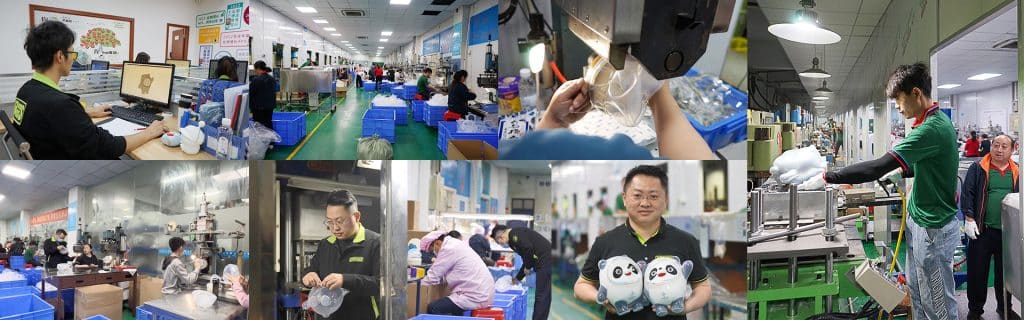