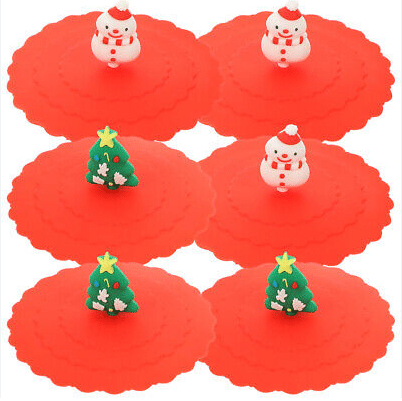
How To Make Silicone lids?
This article mainly introduces the advantages, production equipment, production process, etc. of silicone lids. If you want to create your own silicone lid brand or business and have a clear understanding of the advantages, application areas, design, and production process of silicone lids, please go through this article.
What is the silicone lid?
silicone lids are made of food-grade silicone raw materials. It can be matched with the lids of various coffee cups, water cups or various containers. It has the functions of heat preservation, insect prevention and dust prevention. According to the principle of air pressure, it has a super adsorption function and can effectively seal the cup mouth, which has the effect of leak prevention and heat preservation. Its excellent sealing and dustproof properties make it an ideal sealing material, especially suitable for beverage and food containers that need to be sealed and preserved.
The silicone lid is formed by high-temperature vulcanization of an oil hydraulic press, and according to the stable chemical properties of silicone raw materials, it has high temperature resistance and is 100% environmentally friendly and non-toxic. Silicone lids have passed various environmental certifications, such as FDA, ROHS, SGS, LFGB, etc. BPA free, PVC-free, to ensure the environmental protection and non-toxicity of the lids.
Z.S.R one of the leading manufacturers of different silicone lids for cups, bowls, pots, containers, beakers or Erlenmeyer flasks. Silicone Stretchy Lids and other silicone lids are perfect for on-the-go, spill-free, and drink-safe, Suction Seal. We can supply custom logo, packages and various models added through silkscreen printing, full-color printing.
What are the advantages of silicone lids?
Reusable: Silicone lids have a long service life and can be reused, reducing packaging costs.
Safety: The silicone cover is made of food-grade silicone raw material, which is non-toxic and harmless, suitable for contact with food, and highly safe
High temperature resistance: The silicone raw material has stable chemical properties, can withstand high temperatures, and is safe to use
Environmental protection: The silicone cover has passed various environmental protection certifications, such as FDA, ROHS, SGS, LFGB, etc., to ensure the environmental protection and non-toxicity of the product
Diversity: The silicone cover has a variety of appearances and rich colors to meet the needs of different users
Good sealing performance: The silicone cover has a super strong adsorption function, which can effectively seal the cup mouth and prevent leakage
Z.S.R offers various silicone lids with any shape and colors for different cups, pots, bowls, containers etc
Materials, Tools, Equipment
According to the molded products making process, there are 5 ways of silicone molding process: silicone rubber compression molding, LSR injection molding, silicone Drip molding, silicone Extrusion Molding, silicone Calendaring molding. Here in Z.S.R, For silicone lids, we only have 4 molding process capacity. The different molding process need the different material, tools and equipment:
Silicone compression molding
Silicone Compression Molding
L.S.R injection molding
Liquid Silicone Rubber (LSR) Injection Molding
Silicone Dripping dispensing molding
Multi-Color Dripping Molding
Need prepare silicone as the main material for dispensing molding, usually liquid silicone (LSR) and solid silicone, color paste, vulcanizer, and also need silicone vacuum machine and automatic dispensing machine. As this kind of molding have two kind of molding process. We also call them co-injection molding. Mixed L.S.R material dripping from the automatic dispensing machine first, then heat and curing. Put the solid silicone rubber material on and close the molds put them silicone vacuum machine Vulcanization molding.
The customization process for create your private silicone lids
In Z.S.R, we can custom the silicone lids shape, size, color, pattern, brands, logo by silkscreen printing, full-color printing, or laser engraving for your silicone products, if you would like to custom your brands silicone lids contact Z.S.R.
Appearance (shape, color): The silicone lids Shape can be round, square or creative shape by developing the new tooling. The color can be white, blue, black or use the pantone book number to customized. You also can get mixed color, marble color or double colored, multi-colored appearance.
Material properties: You can customization the material with HTV material or LSR material. The hardness you can choice from 5-80 shore A, Translucent to highly transparent, Safety level from Food Grade to Medical grade, tensile properties from ordinary to high level)
Mold type: Steel, Copper or Al
Molding method: LSR Injection molding, HTV compression molding, dripping molding
Labeling: Logo on the tooling and get the logo products. We also can Screen Printing,Laser Engraving,Heat Transfer Printing your logo on the silicone lids already.
Packaging: zip bag, back card PET box, color box
Shipping method: DHL, FedEx, Air shipping or Sea shipping
How to create your silicone lids brand or start your silicone lids business?
1. Design 3D structure of the silicone lid according to your idea
2. Make the silicone lid tooling according to the silicone lid design requirements (Signal color or multi color) use the different metal, such as steel, copper or AL to ensure the accuracy and durability of the tooling.
Z.S.R International Group (HONG KONG) CO., LIMITED in-house tool shop consists 6 sets of advanced CNC machining centers and 3 sets of EDM spark machines for tooling; So, we can make most of the silicone tooling and repair the silicone tooling in our factory to catch up your time needed.
3. Prepare the silicone lid raw material: Raw silicone material are the key to silicone lid’s products. Usually, silicone lids meet certain environmental protection standards, so silicone lid material are no exception. Normally, environmentally friendly Fumed silicone rubber is selected for customized processing, while many manufacturers use Precipitated silicone rubber for processing.
Although the product is not greatly affected, it is still different Fumed silicone rubber from in quality after a long time. Mix the silicone color according to your silicone lid needed. Cutting the silicone lid material in the correct weight. The color matching principle of the silicone raw materials used in silicone cup lids is basically the same as the color matching principle in art painting.
The white translucent silicone raw materials are combined with the addition of vulcanizers by adding color pastes of corresponding color proportions into them to mix and knead to obtain the corresponding required color. The color matching color is generally based on the international Pantone color card, namely PANTONE color or actual color samples.
4. Feeding the prepared silicone lids mixed material on-Feeding the silicone lid material no matter the Liquid silicone rubber or solid silicone rubber in to the mold.
5. Curing the silicone lid: The silicone lids material is feeding into the mold after mixing, and the silicone lids material is filled into the entire space of the mold through heating and pressure. The temperature, pressure and time control of the molding process directly affect the size, shape and quality of the silicone lids.
No matter the silicone lids was made by: Compression molding or silicone dripping molding or LSR molding.
6. Demolding: After the curing is completed, take the silicone lid product out of the mold.
7. QC the silicone lid: Visually inspect the molded silicone lid to see if there is lack of silicone lid material, uncooked Ness, or impurities
8. Post-processing: Carry out the silicone lid and then do the post processing and treatment, such as trimming, grinding, polishing, spraying, inspection, etc.
9. Secondary vulcanization: Secondary vulcanization is a process that must be handled for any product that has passed the inspection. The main reason why infant silicone lids have a certain smell is that they have not been subjected to Secondary vulcanization baking, and the catalyst of the raw silicone lids material of the products has not been emitted.
At present, many silicone product manufacturers basically handle it, but the time and temperature of the Secondary vulcanization treatment are different. Bake in oven 2-4 hours to meet FDA or LFGB Standard. LSR silicone lid may do not need this process.
10. LOGO or Pattern printing on the silicone lids if needed: screen printing or laser engraving. Most of time, we put the silicone lid logo on the silicone tooling directly.
11. Final Quality control and testing: After all the silicone lid making process finished, we will arrange the final QC for the silicone lid before the delivery.
12. Package and Warehouse: Z. S. R offer custom packaging solutions you need for all your silicone lid packaging. Our custom packaging includes paper boxes, PE/PVC boxes, printed labels, hangtags, barcode stickers, etc to protect the safety of the product during transportation and storage, while ensuring the safety and aesthetics of the product.
In Z.S.R, we manufacture the silicone lid according to the client’s design and idea. We try our best to deliver the quality silicone lid to our customer
When you buy the silicone lid, should pay attention to:
When you would like to buy the silicone lid, you should comprehensively consider factors such as material, safety, brand, Function, and size to ensure a safe.
When you would like to buy the silicone lid, you should comprehensively consider factors such as material, safety, partner, QC, and cost to ensure to fit your needs.
Conclusion
No matter you would like to create the silicone lid with your logo or design for sales, promotional or events. Our high-quality customize silicone lids are perfect for branding, souvenir, corporate gifts.
Z.S.R. customized branded silicone lid with added your logo, design pattern, text may be your good choices.
In Z.S.R, all the steps from raw silicone lids material selection to molding, curing, and quality control, each step plays a vital role in creating your silicone lid that meet safety standards and perform well in their intended applications.
Related Article
How To Make silicone boots?
How To Make Silicone Bowls?
How To Make Silicone Earbud/Earphone Cases?
How to Make Your Silicone Brushes/Scrubbers?
How to Make Silicone Caps: Materials, Tools, Equipment
How to Make Silicone Bags: A Comprehensive Guide from Material Selection to Finishing Touches
How to make air fryer silicone pots or silicone air fryer liner?
Technical Related
About Author: Z.S.R International Group
Z.S.R International Group(Hong Kong) co., Limited, is a one-stop supplier for molded silicone products and silicone products molding solution provider in the consumer products field. We offer OEM services from silicone product design to Silicone products contract manufacturing. We have the capability for custom silicone tooling, LSR(Liquid silicone Rubber) molded silicone products, solid silicone molded products, molded silicone multi-colored products. We also can custom molded silicone, custom molded LSR, custom molded dripping injection dispensing(co-injection) silicone multi-colored products.
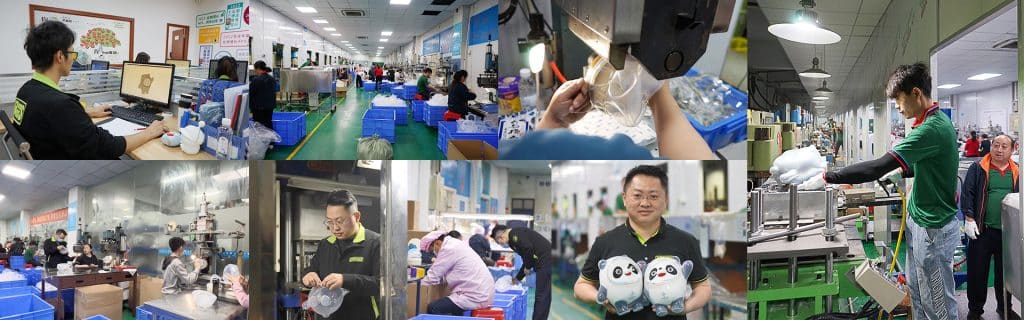