Silicone Printing Guide – How to print Image or logo on silicone
A great way to personalize and advertise your business is to put your logo, text and pattern on silicone rubber products. To print a logo on silicone rubber items. Putting logos or Image on silicone rubber products is a fantastic way to enhance brand visibility and create customized silicone items.
Whether you’re looking to personalize promotional merchandise, create unique silicone corporate gifts, or brand your silicone products, understanding the logo, text and pattern-putting process is essential.
Debossed or Embossed Logo on Silicone Tooling Mold
If you can accept open a new tooling to customize the shapes of your silicone products. The popular and Economy way of put logos or pattern on silicone rubber products is by using debossed or embossed logos on silicone tooling molds. Here’s an overview of the process:
Firstly, Design the silicone tool mold: Work with a skilled tooling engineer to create a mold that incorporates your logo, pattern, text design in a raised (embossed) or recessed (debossed) format.
Then, you need to make the silicone mold tooling production: The tooling mold is fabricated using precision techniques (EDM or CNC) to ensure accurate reproduction of the logo or pattern, and text.
Thirdly, You need to check finished products for logo, text or pattern accuracy, texture and overall quality.
Product Sample
Direct Printing on Silicone Rubber Products Surface
Direct printing is also a good method for putting your logos, text, and patterns on silicone rubber products surfaces. Printed logos or pattern on silicone rubber products is a fantastic way to enhance brand visibility and create customized silicone items without developing new silicone tooling.
Whether you’re looking to personalize promotional merchandise, create unique silicone corporate gifts, or brand your silicone products, understanding the printing process is essential.
In this blog, we’ll provide a comprehensive guide on how to print logos or patterns on silicone products, covering various techniques, including:
1. Laser Engraving
Let’s begin with the Laser Engraving pattern or logo or text on the silicone products: Laser engraving is the process of selectively removing microscopic layers of material, thus creating visible marks on the treated surface.
Depending on the materials, the laser-material interactions can be different. On harder surfaces, the mechanism of action is primarily ablation where the focused beam of laser dislodges microscopic particles from the substrate. Engraving can achieve a depth of 100μm and beyond, whereas laser marking is typically shallower.
The process is suitable for marking logos, barcodes, serial numbers, and QR codes on silicone products. Alongside laser etching, annealing, ablation, and other laser marking technologies, the process forms a set of highly reliable processes in traceability, identification, and product decoration.
2. Silkscreen Printing
Screen printing is a printing technique where a mesh is used to transfer ink (or dye) onto silicone products, except in areas made impermeable to the ink by a blocking stencil. When the screening has been completed, an operator will then pour ink onto the screen, pushing it through the stencil.
The ink will only ever go where the stencil is open. This helps to create a printed design for a logo, pattern, or text. A stencil is used on the screen to develop the graphic, with a mesh being stretched over a wooden or metal frame. A blade or squeegee is moved across the screen to fill the open mesh apertures with ink, and a reverse stroke then causes the screen to touch the substrate momentarily along a line of contact.
This causes the ink to wet the substrate and be pulled out of the mesh apertures as the screen springs back after the blade has passed. One color is printed at a time, so several screens can be used to produce a multi-colored image or design.
3. Pad Printing
Pad printing, also called tampography or tampo printing, is an indirect offset (gravure) printing process where a silicon pad takes a 2-D image from a laser engraved (etched) printing plate (also called cliché) and transfers it to 3-D products.
It is printed by machine with a metal plate. The plate is flat, with the image chemically imprinted. The silicone pad is pressed onto the ink, picking up the image. And then the silicone pad is pressed onto the substrate, transferring the image on the silicone product.
The advantage of pad printing is that the printing speed is fast, and you can print several colors at the same time. Pad printing can be used on a variety of substrates, particularly oddly shaped objects that are difficult to screen print. They can print all kind of difficult-shaped products such as curved (convex), hollow (concave), cylindrical, spherical, compound angles, textures, etc. which were not available with traditional printing processes.
4. Water Transfer Printing
Water transfer printing, also known as immersion printing, water transfer imaging, hydro dipping, water marbling, cubic printing, Hydrographics, or Hydro Graphics. It is a decorative coating technology that allows you to apply detailed patterns and artwork onto 3-dimensional objects. It allows a manufacturer or brand to make silicone parts or silicone products with virtually unlimited appearance options.
It allows you to apply an elaborate graphic such as carbon fibre, wood grain and even camouflage onto a product. The great thing about this is that it can be applied to a 3D product surface. The water transfer printing process is extensive, and it can be used to decorate items that range from vehicles to any silicone items.
To begin with, we will place a water-soluble film onto the surface of the water. We will then immerse the product into the liquid bath, with pressure created being used to wrap the item.
5. Heat Transfer Printing
Heat transfer printing is a popular printing method used to create designs for the decoration, pattern, logo, text on silicone products. Heat transfer, also known as thermal printing, thermal-transfer printing and thermal-wax transfer, is a method of printing that allows you to print a design onto an object.
Heat transfer printing uses the process of heat to transfer an image created in wax to an object or garment. This printing method is compatible with pre-painted images on a wax sheet or can be used to create an image by layering wax dye onto an object.
This printing method involves using heat and pressure to transfer a design onto the silicone surface, resulting in a permanent bond between the design and the material.
6. In-Mold Decoration
In-mold decorating (IMD) is a process of labeling or decorating molded Silicone products or components during the molding cycle. The label, logo, or pattern becomes an integral part of the final product, creating a fully decorated item at the molding press.
In this process, a pre-printed label or decorated film is inserted in the open silicone compression or injection mold and held in place via vacuum ports, electrostatic charge or another method. When the mold is closed, the Silicone resin is injected into the mold, encapsulating the label permanently within the finished products.
In-mold decoration technology gives you the freedom to design elaborate, colorful graphics and integrate them with your product. Through years of research and development, we have perfected a method that is effective, reliable and economical.
7. Digital Color Printing
Digital printing is a method of printing from a digital-based image directly to a variety of media. It usually refers to professional printing where small-run jobs from desktop publishing and other digital sources are printed using large-format and/or high-volume laser or inkjet printers.
Print on silicone products then you may want to print photos, pictures, logos or even text. The requirements for silicone printing are high and for this reason, quality equipment is key. After printing, the product has to be robust in use, and it also needs to be resistant to scratches and abrasions. Chemical resistance to detergents may also be a desirable feature.
Digital printing is the process of printing digital-based images directly onto a variety of media substrates such as silicone. There is no need for a printing plate, unlike with offset printing. Digital files such as PDFs or desktop publishing files can be sent directly to the digital printing press to print on paper, photo paper, canvas, fabric, synthetics, card stock and other substrates. it is possible to print on silicone items individually.
Considerations for Printing Designs on Silicone Products
As we all know printing your company’s logo on silicone rubber products is a fantastic way to personalize and promote your brand. Please use the following straightforward procedures to print a logo, text, pattern on silicone rubber products:
Select a Printing Technique Printing Method: When it comes to printing silicone rubber products, there are a number of options available, including Laser engraving, screen printing, pad printing, heat transfer printing, water transfer printing, In-Mold Decoration and digital color printing. There are several techniques you can use to print silicone rubber products, Choose the approach that best meets your needs among them because each has positive effects. Since they all have advantageous impacts, pick the one that best fits your demands.
Create the Artwork: Before manufacturing your logo, you must have artwork that is the correct size and resolution. The artwork can be created using any design program; just be sure to save it in a file format that is compatible with the printing process you intend to use.
Clean the Silicone Rubber Surface: Clean the silicone rubber products with a treatment agent. Make sure the silicone rubber products surface is clean, dry and free from any contaminants.
Printing the logo, text or pattern: You can start printing promptly as long as your ink, design, and surface have been prepared. You must use the printing equipment according to the directions provided by the method you select.
Curing or Drying: After printing the logo, the ink needs enough time to dry or be cured to ensure that it doesn’t smear, crock, or rub off. You can leave the silicone rubber product in a controlled environment or use a curing oven that dries the ink quickly.
Lastly, Check finished products for logo, text or pattern color, accuracy, texture and overall quality.
Conclusion
Print logos, pattern, text on silicone rubber products allows you to create customized silicone items that reflect your brand identity and enhance brand recognition. When you choose the printing way to put your design on understanding the printing process and considerations is crucial for a successful logo application.
Evaluate your logo design, product requirements, and budget to determine the most suitable printing technique. By investing in quality logo printing, you can elevate your brand and create impactful silicone rubber products that stand out in the market.
Related Blog
Technical Related
About Author: Z.S.R International Group
Z.S.R International Group(Hong Kong) co., Limited, is a one-stop supplier for molded silicone products and silicone products molding solution provider in the consumer products field. We offer OEM services from silicone product design to Silicone products contract manufacturing. We have the capability for custom silicone tooling, LSR(Liquid silicone Rubber) molded silicone products, solid silicone molded products, molded silicone multi-colored products. We also can custom molded silicone, custom molded LSR, custom molded dripping injection dispensing(co-injection) silicone multi-colored products.
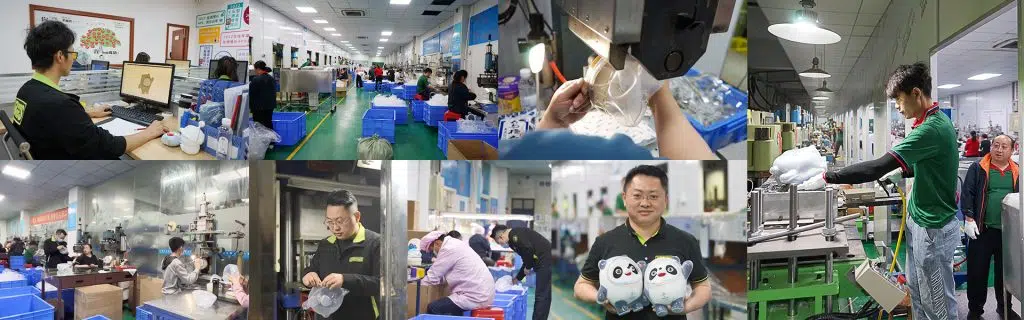